Altium
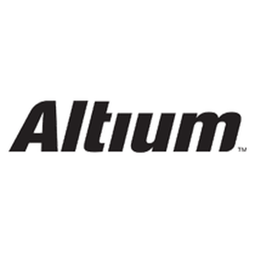
Overview
HQ Location
United States
|
Year Founded
1985
|
Company Type
Public
|
Revenue
$100m-1b
|
Employees
201 - 1,000
|
Website
|
Stock Ticker
ASX: ALU
|
Twitter Handle
|
Company Description
Altium Limited develops and sells computer software for the design of electronic products. The company offers products in the domains of PCB implementation, FPGA design, Embedded Software development, and design data management for individual engineers, small teams, and enterprises.
Key Customers
Accuphase Laboratories, Agilent-Qianfeng Electronics Technologies ANCA, Bang & Olufsen
IoT Snapshot
Altium is a provider of Industrial IoT platform as a service (paas), processors and edge intelligence, sensors, actuators, functional applications, networks and connectivity, analytics and modeling, application infrastructure and middleware, other, wearables, infrastructure as a service (iaas), drones, and robots technologies, and also active in the aerospace, automotive, buildings, cement, chemicals, consumer goods, education, electrical grids, electronics, equipment and machinery, food and beverage, glass, healthcare and hospitals, marine and shipping, plastics, renewable energy, semiconductors, telecommunications, and transportation industries.
Technologies
Use Cases
Additive Manufacturing
Autonomous Robots
Building Automation & Control
Chatbots
Construction Management
Experimentation Automation
Facial Recognition
Indoor Air Quality Monitoring
Inventory Management
Last Mile Delivery
Leasing Finance Automation
Manufacturing Process Simulation
Material Handling Automation
Outdoor Environmental Monitoring
Predictive Maintenance
Predictive Waste Reduction
Rapid Prototyping
Real-Time Location System (RTLS)
Remote Collaboration
Service Parts Management
Smart Campus
Smart Parking
Time Sensitive Networking
Track & Trace of Assets
Vehicle Performance Monitoring
Virtual Prototyping & Product Testing
Virtual Reality
Visual Quality Detection
Water Utility Management
Functional Areas
Industries
Services
Technology Stack
Altium’s Technology Stack maps Altium’s participation in the platform as a service (paas), processors and edge intelligence, sensors, actuators, functional applications, networks and connectivity, analytics and modeling, application infrastructure and middleware, other, wearables, infrastructure as a service (iaas), drones, and robots IoT Technology stack.
-
Devices Layer
-
Edge Layer
-
Cloud Layer
-
Application Layer
-
Supporting Technologies
Technological Capability:
None
Minor
Moderate
Strong
Supplier missing?
Start adding your own!
Register with your work email and create a new supplier profile for your business.
Case Studies.
Case Study
Enhancing Oceanic Research with IoT: A Case Study on Monterey Bay Aquarium Research Institute
The Monterey Bay Aquarium Research Institute (MBARI) has been conducting extensive research on our oceans for over three decades. Their studies range from examining the axial seamount and the active submarine volcano along the Juan de Fuca Ridge off the coast of Oregon to studying methane and hydrocarbons in mud in the Arctic. The research is crucial for understanding the extent of climate change, focusing on the biologic response of stressors to the oceans. However, the process of studying these changes, which involves deep-water mapping three to four thousand meters below the ocean surface, collecting sonar data, and measuring turbulence and bioluminescence up to 150 days per year, is challenging. MBARI uses its proprietary technology, including long-range autonomous underwater vehicles (LRAUVs), to conduct these studies. However, designing these LRAUVs and packing them with ample capabilities within a small space, including 5000-watt lithium-ion batteries encased in air-tight sheet metal pressure housing, is a complex task.
Case Study
Ending Energy Poverty: Bboxx's IoT-Enabled Solar Power Solution
Energy poverty, defined as the lack of access to modern energy services, affects over 840 million people globally. An additional billion people are connected to unreliable power grids, leading to connectivity losses that negatively impact both public and private sectors. Bboxx, a next-generation utility company, aims to address this issue by manufacturing, distributing, and financing decentralized solar-powered systems in developing countries. However, the company faced challenges in developing hardware units that are compact, easy to use, and capable of transforming solar energy into raw power. The design process required multiple iterations and collaboration among various team members, including electrical and mechanical engineers.
Case Study
Greening PCBs with SODAQ and Altium: A Case Study
SODAQ, a Netherlands-based company, has been focusing on creating greener Printed Circuit Boards (PCBs) for over seven years. They design hardware and software for a variety of applications, including smart desks and bikes that measure air quality. Their first product, a solar-powered weather station, established them as pioneers in green technology. However, as their designs became more complex, integrating GPS tracking and solar power, they faced challenges. Designing complex PCBs with integrated solar panels required professional design tools. Their non-solar designs, like office desks that can track occupancy, featured custom applications that surpassed the limitations of most PCB design software tools. Managing components and design libraries with their old ECAD software was challenging, and collaboration between mechanical engineers and PCB designers was difficult.
Case Study
Perfect Sound Forever: Teenage Engineering's Synthesizers and Altium's CoDesigner
Teenage Engineering, a Swedish company, specializes in creating compact, powerful synthesizers, including a series of small, battery-powered synthesizers known as pocket operators. These devices, which are roughly the size of a pocket calculator, can be connected together to produce and record a variety of music genres. The company's mission is to make synthesizers accessible to everyone, with a simple interface, animated LCD displays, and affordable price points. However, the design process of these devices presented a challenge. The company handles everything in-house, from electrical and mechanical engineering to industrial design and software development. The main challenge was getting the balance right between ECAD and MCAD software tools. The company's designs usually start on the MCAD side, building up the overall electromechanical look and feel. An ultra-tight tolerance chain was key when bouncing designs back and forth between Altium and MCAD.
Case Study
Transforming PCB Design with Altium Designer and Altium 365: A Case Study
Small PCB design firms often face the challenge of limited access to affordable, comprehensive software tools. These tools are essential for designing, co-designing, sourcing parts, and sharing projects at each stage of the development cycle. Many available tools are incomplete, requiring additional modules that increase complexity and costs. Matthew Lightsey, founder and principal designer of Granite Summit Designs, experienced this challenge firsthand. His firm specializes in designing custom PCBs for various industries, including commercial, industrial, aerospace, and defense. When starting his own design firm, Matt did not want to compromise on professional tools. However, he found that more comprehensive solutions came with a higher price tag, while cheaper solutions were inadequate for professional use.
Case Study
SpaceQuest's Transformation with Altium Designer: A Leap into Advanced Satellite Technology
SpaceQuest, a satellite technology company, was facing challenges with their PCB layout on complex designs and often had to outsource projects. With a major microsatellites program on the horizon, they needed a more efficient solution. They were also in the process of developing microsatellites for asset tracking and management services from low earth orbit and exploring how to collect AIS signals from space. However, their preliminary design of a payload to collect AIS signals was still a prototype and their development processes were evolving. In a critical situation, they had to integrate a brand new payload relatively late in a satellite development project, with only six weeks remaining before the design was scheduled to ship for launch. The task of delivering a completely new electronic board on such a tight schedule using their previous tools and processes was daunting.
Case Study
Revolutionizing Patient Rehabilitation with Harmonic Bionics' Harmony SHR
The World Health Organization estimates that hundreds of millions of people suffer from over 600 different neurological disorders, including strokes, Alzheimer’s disease, epilepsy, Multiple Sclerosis, and Parkinson’s disease. In 2017, the global prevalence of strokes alone was 104.2 million. For survivors, the road to recovery is challenging and requires extensive rehabilitation with the continued assistance of therapists, doctors, and clinicians. To regain motor functions after suffering strokes or other sudden onset conditions that can cause brain or spinal cord injuries, repetitive motions are essential to help patients regain neuroplasticity. However, this task is daunting for both therapists and patients, requiring a significant amount of time and effort.
Case Study
Revolutionizing Solar Energy Production with Morgan Solar and Altium
Morgan Solar, founded in 2007, has been on a mission to make solar energy the most widely used and affordable power source in the world. However, the solar market has been changing rapidly, with product costs decreasing significantly over the past decade. This has increased the urgency for Morgan Solar to develop and patent newer, more efficient solar energy solutions. The company has had to consistently innovate to keep up with the fast-paced industry and stay ahead of the curve. The challenge was to accommodate less forgiving production timelines and increase product turnover, while maintaining the quality and efficiency of their solar panels and solar tracking systems.
Case Study
Altium Designer and Altium 365: Empowering Global Collaboration for Open Source Ventilator Project
The global pandemic has put an unprecedented strain on the healthcare industry, particularly on the medical supply chain. One of the most critical needs has been for ventilators, which are expensive and time-consuming to manufacture. The Open Source Ventilator Project, a global coalition of engineers, designers, and medical practitioners, rose to this challenge by creating low-cost Field Emergency Ventilators (FEVs) using 3D-printed components. However, the project faced significant challenges in terms of collaboration and coordination. With over 3000 volunteers from different companies, individual engineers, medical device designers, and programmers from all over the world, the project required a platform that could facilitate seamless collaboration and sharing of PCB designs.
Case Study
Owning the PCB Design Process: A Case Study on CAS Tecnologia and Altium
CAS Tecnologia, a São Paulo-based technology firm, was struggling with its PCB design process. The company, which applies scientific and engineering principles to improve efficiency across a wide range of government services, environmental, financial, and telecommunication projects, was heavily reliant on outsourcing to complete critical parts of a product design process. This dependence on other companies was hindering their financial success and future growth potential. To continue growing in the intelligent automation and telemetry industry, CAS needed to bring all of their design processes in-house for complete control and independence. A significant aspect of their restructuring required integrating an electronics design process into their existing mechanical workflow.
Case Study
Breville's Process Speed Boost with Altium 365 Pro
Breville, a global kitchen products brand, was facing challenges in its design facility in Sydney. The facility, staffed by around 200 professionals, required a high degree of flexibility to support its fast-paced business. The biggest problem was communication. Information was disseminated through multiple channels, leading to reduced efficiency and difficulty in completing projects on time. The communication between the designer and the manufacturer was inconsistent, leading to issues with ensuring the correct revision drawings were used. Additionally, the manufacturer would select components based on solutions that worked for them, which may not have been the best fit for the specific project.
Case Study
Bosch Rexroth's Green Engineering Success with Altium Designer
Bosch Rexroth, a Fortune 100 company and one of the world’s largest suppliers of technology and services, has been committed to sustainability and green engineering practices for nearly half a century. The company recognizes the potential of green engineering to reduce costs, improve product performance, enhance corporate reputation, and open up new market opportunities. However, to truly be considered 'green', engineers must consider factors such as product life cycle, reusability, and the elimination of toxic chemicals. Bosch Rexroth’s engineering division faced the challenge of designing its latest Rexroth Frequency Converter Fe series to be more economical and environmentally friendly. The goal was to reduce parts, size, and power consumption, while improving reliability and stability.
Case Study
Altium Empowers BattleBot Design and Scalability: A Case Study
Ricky Willems, an electrical engineer and a fan of the popular show “BattleBots”, was inspired to build his own robots with the goal of competing on the show. The challenge was to create a mechanical warrior that could compete in the show, which required custom hardware, electronics, and a team of up to eight people to operate the bots. The design process was complex, involving the creation of a 6’4”, 250 lb flame-throwing robot capable of catapulting another robot across a ring. The design also needed to be scalable, as the robots needed to prove their worth on smaller stages before moving to prime time. The design process was further complicated by the need for the robot to withstand damage while putting out staggering horsepower in a package that was as light and small as possible.
Case Study
Reviving Old Ideas with New Technology: Automation Research Group's Journey
Automation Research Group, a Philadelphia-based engineering and design company, was facing challenges in managing and transmitting data securely. With the advent of high-speed internet, data transmission became faster but also brought along security concerns. For some clients, having a private network tethered to a building was more secure than using WiFi or broadband internet connections. This led the company to revisit the idea of using power lines as an alternative to WiFi for data transmission. However, this method, while more secure, was slower and required specialized equipment. Additionally, the company was also struggling with managing parts for their custom-designed PCBs. The parts management was all in a local database and there was no way to determine if the parts were outdated.
Case Study
Empowering Innovation with Altium Designer: A Case Study on Accuphase Laboratories
Accuphase Laboratories, a respected manufacturer of high-performance audio products based in Yokohama, Japan, faced a significant challenge in maintaining the quality and consistency of their circuit board production. The company's iterative design approach, which is based on sequential circuit refinement in response to both subjective and objective performance testing, resulted in the creation of many prototypes. This process led to short, critical PCB design cycles for Accuphase’s engineers. To maintain their high standards, Accuphase needed to complete all phases of their board-level design in-house while maintaining the highest possible quality. The demands of the high-end audio equipment industry, akin to the limited-production luxury car market, placed high demands on both their design engineers and the electronic product development software they used. Production volumes were low, research and development was a primary focus, and design quality was never compromised.
Case Study
Enhancing Electronics Design and Collaboration with Altium Technology: A Case Study on Quantel Laser
Quantel Laser, a division of Lumibird and a global leader in laser technology, has been facing increasing challenges in meeting the evolving needs of its customers. The company, which develops solid-state lasers, laser diodes, and fiber lasers, has seen its customer needs become progressively more intricate over the years. The industry has shifted from a highly specialized technical field to one that powers a wealth of everyday essentials. The demand for more energy in a smaller size at a lower cost has pushed the company's skills to the max. The company's engineers have relied on Altium technology for decades to meet these demands. However, the advent of the global pandemic posed a new challenge for the company, as it impacted their offices in France and the United States, disrupting their design team's ability to work together.
Case Study
Driving Greater Energy Efficiency: UNSW’s Sunswift Racing and Altium
The University of New South Wales’ (UNSW) Sunswift Racing team, led by Professor Richard Hopkins, has been competing in the Bridgestone World Solar Challenge since 1996. This race, which spans the Australian Outback from Darwin to Adelaide, showcases solar-powered, custom-built cars. The Sunswift Racing team, made up of 45 undergraduate students across multiple engineering disciplines, has designed and built 6 solar-powered hybrid vehicles. Their most recent vehicle, the VIolet, ranked 2nd in the 2019 Bridgestone World Solar Challenge and set a new Guinness World Record for Lowest Energy Consumption in 2018. However, the team faced a setback when the 2021 Bridgestone World Solar Challenge was cancelled due to the Covid-19 pandemic.
Case Study
Developing Cutting-Edge Wireless Technology with NuCurrent and Altium Concord Pro
NuCurrent, a company known for its patented wireless inductive technology, faced a significant challenge as it grew. The company's technology is found in a variety of everyday essentials, from PopSockets® to smart basketballs and kitchen countertops. However, as the company expanded, it became clear that they needed a professional solution for PCB component library management and version control. Their existing system, GitHub, was proving to be inadequate for their growing needs. The lack of synchronization in GitHub made it difficult to reuse parts across multiple projects and changes were not getting propagated. This often resulted in issues being caught later in the development cycle, causing delays and inefficiencies. Furthermore, the company was using Google Drive and emailing files to clients, which created serious version control issues.
Case Study
Leveraging IoT for COVID-19 Treatment Development: A Case Study of MKS Instruments and Altium 365
MKS Instruments, a leading provider of mass spectrometers and other essential laboratory equipment, was facing a significant challenge amidst the COVID-19 pandemic. The company, which holds over 2,500 patents and employs over 500 degreed scientists and engineers, was under immense pressure to support the urgent need for the development of treatments for COVID-19. The situation was further complicated by stay-in-place orders, which made it difficult for MKS's engineering team to work around the clock from anywhere. The company needed a solution that would allow them to keep up with the frenetic pace of work, while also ensuring the availability of parts for their devices, which are used in labs worldwide.
Case Study
Revolutionizing Space Exploration: Curtin University's Binar-1 CubeSat Project
The Binar team at Curtin University's Space Science and Technology Centre aimed to create a custom-designed CubeSat that was smaller and more effective than the existing miniature satellites. The challenge was to build a CubeSat from scratch, as most universities traditionally use kits made in the US or Europe. The team believed that designing their own CubeSat would provide a more enriching learning experience and inspire others to take a similar approach. They aimed to reduce the space inside a CubeSat to create a more lightweight and powerful device. The initial designs were between 2U and 3U, but the team wanted to reduce this to just 1U. The goal was to fit all the systems designed at Curtin University onto a single PCB that could fit in their 1U CubeSat.
Case Study
APTUS DesignWorks Accelerates Innovation with Altimade
APTUS DesignWorks Inc., a product development and machine design services provider based in Maryville, Tennessee, was facing challenges in accelerating project times and delivering quality service to their customers faster than their competitors. Despite their best agile practices, collaboration tools, and in-house iterative processes, they realized they needed external resources to provide them with substantial advantages in terms of price and lead time. The company was also struggling with the manufacturing approval phase and product launch, which was slower than desired. Before Altimade, they used to order the bare boards and components separately to produce a prototype, which was either assembled in-house or outsourced to a third party. Both methods required considerable time and resources.
Case Study
Future Tech with Flight Circuits and Altium: A Case Study
Adam Gerken, the founder and president of Flight Circuits, has been designing complex, futuristic devices for his clients from his studio in Rochester, New York. His creations range from battery-powered medical pump controllers to wearable asthma monitoring systems, palm-sized single-board computers, and a small, sleek ring that replaces keys, credit cards, and passwords with personalized security. He has also begun to develop compact wireless receivers for use in machine learning and continuous monitoring devices. However, Adam's peers often struggle with legacy systems and complex programs that hamper the development process. Adam needed a reliable, efficient, and advanced tool to design simple and complex PCBs for his various projects.
Case Study
Revolutionizing Golf Training with Foresight Sports and Altium
Foresight Sports, a San Diego-based company, is known for its sophisticated golf data collection tools that help golfers and teaching professionals improve their game. The company's systems, which include portable launch monitors and indoor golf simulation systems, use high-speed cameras to capture a series of images during the first several inches of ball flight. These images are then analyzed to measure speed, launch angle, and spin. However, the design of these devices, particularly the GCQuad and the GCHawk, posed significant challenges. The GCQuad, which used the framework of two existing products, required four different rigid-flex boards and an unusual design to fit inside its upright, hourglass-shaped chassis. The GCHawk, on the other hand, had to accommodate a six-layer rigid-flex board, three circuit-layer boards, a 14-layer high-speed board, and a two-layer LED board with an indicator, all within a narrow space.
Case Study
Revolutionizing Electronic Product Design: A Case Study on YASA Ltd.
YASA Ltd., a British manufacturer specializing in electric motors, controllers, and powertrain solutions for hybrid and electric automotive applications, faced a significant challenge. The increasing demand for hybrid and electric automobiles, coupled with a renewed interest in greener aviation solutions, necessitated continuous innovation from YASA's engineering team. The company had always invested in remote working tools, but the full value of these investments became apparent during the pandemic. The lockdown posed a significant challenge to their design teams, who needed to continue collaborating seamlessly despite the physical distance and restrictions.
Case Study
Smart PCB Design Solutions with Kinetic Vision and Altium 365
Kinetic Vision, a Cincinnati-based design, engineering, and development firm, is a one-stop-shop for innovators looking to transform their ideas into real products. The company offers a wide range of services, including industrial design, mechanical and electrical design and engineering, hardware and software development, machine learning, visual communication media, prototyping, and sometimes even short-run production. However, finding the right tools for PCB design had been a challenge for them over the years. They needed a solution that could support the production of smart products that incorporate electronics, PCBs, and communications chipsets. The solution needed to be versatile enough to handle all of their projects, from the simplest to the most advanced.
Case Study
Bridging the Gap Between Designers and Customers with IoT
The process of transforming great ideas into real, physical electronic products involves a team of talented individuals and multiple companies. One of the key challenges in this process is the communication of PCB designs with customers. This is often difficult as visualizing the board’s development can be somewhat esoteric. Furthermore, the process of designing electronic systems can take upwards of a year and a half or more, making it challenging to explain to customers where their projects are in the pipeline. It’s difficult to share schematics and part placement during the development cycle. Paul Payen de la Garanderie, Founder and Owner of AW Audio, an engineering services company based in France, understands these challenges very well. He has had to work with multiple companies over the years, from small start-ups to celebrated AV firms, and is all too familiar with these challenges.
Case Study
Rocketing into the Future with Apollo Fusion and Altium
Apollo Fusion, a Bay Area startup, develops propulsion systems for satellites that provide global connectivity. Their Power Processing Units (PPUs) are built to withstand the harsh environment of space, being rugged and radiation-tolerant for ongoing operation inside thermal vacuum chambers or in orbit around the earth. However, to ensure that their PPUs can hold up under extreme conditions, Apollo Fusion has to test their propulsion systems for just about everything, from radiation, to shock, and random vibration. The electronic components, including the PCBs, have to withstand the rigorous testing. As a startup company, maintaining a level of transparency is essential from an investment perspective. With the first major launch on the immediate horizon, Apollo Fusion needed to find a way to connect their R&D team, management and investors quickly and easily, ensuring all key stakeholders had the most accurate, up-to-date information on product development.
Case Study
21st Century Coffee Breaks: Animo's IoT Journey with Altium
Animo, a commercial coffee equipment company based in The Netherlands, has been a leader in the European commercial coffee dispensing market for over 70 years. Their products, ranging from traditional filter coffee pots to award-winning touchscreen systems, are sold in over 70 countries. However, with the increasing complexity of their designs, particularly in their OptiLine series, Animo faced challenges in developing their products. The OptiLine series, which includes the OptiVend, OptiFresh, OptiBean, and OptiMe, are designed for convenience and elegance, with features such as touchpads and the ability to yield up to 1250 cups of coffee daily. The first-generation OptiLine devices were created using freeware PCB software, but as designs became more complex, Animo began working with external firmware development houses that relied on Altium Designer. This shift to external development houses presented a challenge for Animo in terms of control and efficiency in their product development process.
Case Study
Revolutionizing Sustainability: Woodoo and Altium's Innovative Approach to Material Development
Woodoo, a Paris-based materials company, is on a mission to redefine sustainability by transforming responsibly-harvested hardwoods into a durable, translucent material. The company uses a proprietary nanotechnology process to remove lignin from wood and replace it with a bio-based polymer made from recycled materials. The resulting product is as versatile as plastic, but thinner, stronger, and more translucent. However, in the early years of operation, Woodoo relied on a free PCB design tool that was insufficient for their growing needs. By 2020, it was clear that a more comprehensive solution was needed to meet the company's ambitious goals. The challenge was to find a new PCB software tool that would support the company's progress and clients with ease.
Case Study
Streamlining In-house PCB Design with Sanden Vendo: An IoT Case Study
Sanden Vendo America Inc., a Dallas-based company known for designing, manufacturing, and selling innovative vending equipment, faced a significant challenge. The company, which has been in operation for nearly a century, had always relied on specialized vendors and contractors for the design of their machinery. However, to maintain their leading position in the market, they realized the need to move their electronic design process completely in-house. This transition required finding electronic design automation tools that would not only facilitate their innovative designs but also avoid production delays or compromises in quality control. The challenge was compounded by the fact that they were first-time users of electronic design software, and the software would be used by their existing engineering department staff, not a dedicated PCB design specialist. Therefore, the software needed to be intuitive and easy to use, with excellent customer support from the vendor.
Case Study
Streamlining Semiconductor and Sensor Solutions Development with Altium Designer: A Case Study on AustriaMicrosystems
AustriaMicrosystems (AMS), a company with over 30 years of experience in designing and manufacturing advanced analog sensor solutions, was facing significant challenges in their development process. Their customer base, under pressure to deliver increasingly complex products in shorter time frames, relied on AMS to provide component reference designs, application samples, and sensor technologies that worked flawlessly. However, AMS was struggling to meet these expectations due to errors in their development process that were affecting their customers. The issues stemmed from AMS's reliance on multiple sets of software for their in-house electronic design, leading to data conversion and exporting issues, and corrupted databases. The existing systems were causing more harm than good, and it was clear that a unified design solution was needed to integrate their entire workflow under one common thread.
Case Study
Planning for the Future with Cirris Systems and Altium
Cirris Systems, a major leader in the cable testing sphere, faced a significant challenge in finding the right eCAD software tools. The company had struggled with six different software platforms before considering Altium Designer. The need for a tool that would support their team and their eventual replacement was crucial. Furthermore, the company had to meet the rigorous cable testing requirements of various industries, including government, defense, and aerospace firms. This necessitated tight revision control and process tracking, which was difficult to manage with their existing systems. The situation was further complicated by the sudden onset of the COVID-19 pandemic, which forced the company to transition from onsite to remote work almost overnight.
Case Study
Leveraging Altium Designer for Satellite Design at RWTC Aachen University
RWTC Aachen University, the largest technical university in Germany, presented its students with a unique challenge to develop a space-ready satellite that can withstand the harshness of space and a return into earth’s atmosphere, all while keeping development costs as low as possible. This project was an opportunity for students to gain hands-on experience in the spacecraft engineering discipline, learning valuable management and technical skills as they juggled the responsibilities of mechanical, electrical and systems engineering and the complexities of project management. The development of the innovative satellite system, named COMPASS-1, came with a strict set of design restrictions. Students had to meet requirements as defined by the international CubeSat standards, including shape and weight restrictions as well as using only commercial, off-the-shelf components while controlling production costs.
Case Study
Revolutionizing Coffee Making with IoT: Luminaire Coffee, La Marzocco and Altium
Luminaire Coffee, a Seattle-based startup, was driven by the mission to help baristas and coffee aficionados craft the perfect cup of coffee with efficiency and ease. They identified a gap in the coffee preparation sphere and sought to fill it with innovations such as shot timers, flow measuring scales, and a special heating device. Their efforts led to a partnership with La Marzocco, a renowned manufacturer of espresso machines. The challenge was to create the most intuitive, foolproof machines on the market, integrating Luminaire Coffee’s designs into the core of the Linea LB, La Marzocco’s most technologically advanced espresso machine. Luminaire Coffee needed to create next-generation electronics for the Linea PB, including its shot timer, temperature control functionality, flow pulse counter, and integrated scale. The challenge was to divide up work across the team so that multiple engineers could work on a single project at once, designing to different EMC and manufacturing standards.
Case Study
Revolutionizing Underwater Robotics Design with Altium
Bluefin Robotics, a pioneer in the field of Autonomous Underwater Vehicles (AUVs), faced significant challenges in coordinating electrical and mechanical designs due to the tight design requirements of their AUVs. The existing sequential process of electrical to mechanical design was proving to be inefficient and cumbersome. Engineers were forced to rely on cardboard models, which limited their ability to fully visualize their work and requirements. The AUVs, which are completely autonomous and navigate the seabed to collect data and images, had to be designed to withstand extreme conditions, including pressures of up to 6000 pounds per square inch at depths of 4000 meters. Furthermore, the vehicles had to be neutrally buoyant to reduce propulsion energy requirements and increase efficiency. This meant that for every cubic inch of air added to the vehicle, an equivalent amount of weight had to be added, leading to a delicate balance between performance, buoyancy, and reliability.
Case Study
High-Tech US Defense Contractor ITT Corporation Switches to Altium Designer for Complex Re-Engineering Projects
The Systems Division of ITT Corporation, based in Colorado Springs, USA, is a prime contractor on the US defense program. The division is tasked with sustaining the service of operational systems through progressive re-engineering under the System Engineering and Sustainment Integrator (SENSOR) program. This program covers the Air Force Space Command’s worldwide network of Missile Warning, Missile Defense, and Space Surveillance systems. One of the key projects under this program is the re-engineering of signal processing systems in the AN/FPS-85 phased-array radar system based at Eglin Air Force Base in Florida. The radar system, commissioned in the late 1960s, used cutting-edge technology of its time and offered unprecedented tracking capabilities and performance. The current re-engineering process aims to implement the latest technology and techniques to create signal processing electronics that will be at the cutting-edge when the system is commissioned in 2010. This forward-thinking development process places high demands on the ITT development team and the tools they use to create the new signal processing subsystems and operational software.
Case Study
Bosch: Pioneering Green Engineering with IoT
Large corporations are increasingly under pressure to address environmental concerns while maintaining their business operations. The challenge lies in the perceived trade-off between corporate strategies and environmental responsibility. Many organizations struggle to see the opportunities in green engineering, while others are simply confused by the numerous principles and guidelines that can differ for each industry and organizational department. For instance, electronics engineers can influence the impact of their products by adhering to various design principles such as green engineering, sustainable design, green design, or design-for-environment. These principles share the same basic rules: make it smaller, more reliable, and consume less power. However, engineers must also consider product life cycle, reusability, and how to eliminate toxic chemicals before they can start touting themselves as ‘green engineers’.
Case Study
Innovation and Efficiency in Design: A Case Study of Bang & Olufsen
Bang & Olufsen, a renowned manufacturer of high-quality audio, video, and multimedia products, faced a unique challenge in its 'ideas factory'. The 'ideas factory' is the birthplace of most of the company's electronic designs, where prototypes for the next generation of audio, visual, and mobile communication systems are created. The challenge was dealing with the multitude of options and changes that each prototype presented. Every new prototype was akin to a blank canvas, and the real test was finding the appropriate architecture for the board. Additionally, the company's unique mechanical casings presented a significant challenge for the designers. The process of changing and redesigning components, re-evaluating design media, and making trade-offs was complex and time-consuming.
Case Study
Accuphase Laboratories: Enhancing Audio Product Quality with Altium Designer
Accuphase Laboratories, a renowned Japanese manufacturer of high-end audio products, faced a challenge in maintaining the quality and consistency of their circuit board production while reducing research and development time cycles. The company operates in a specialized industry similar to the luxury car market, where product development is focused on innovative, high-quality design rather than low-cost production. Accuphase does not release a regular stream of new products like mainstream consumer electronics companies, but it does respond to customer needs by bringing new and innovative products to market as quickly as possible. This approach requires an extremely iterative design process based on sequential circuit refinement in response to both subjective and objective performance testing. As a result, many prototypes are built, tested, and auditioned through the development process, creating short, critical PCB design cycles for the Accuphase engineers.
Case Study
Designing PCBs for Mars: DKB Resources' Complex Design Process Management
DKB Resources, a successful electronics service bureau, has carved a niche in developing specialized Printed Circuit Boards (PCBs) for organizations in the space and military industry. However, this commitment comes with a significant responsibility. The company must work within the strict requirements of its clients, design using specific sets of standards and guidelines, and ensure that its designs can withstand harsh environments like space. This necessitates a strong emphasis on quality, reliability, documentation, and good communication with clients. The company's work is checked by program managers, procurement managers, and administrative support managers, each with their own data requirements and document standards. This complex process is likened to being multilingual by Darya Bronston, President of DKB Resources. The company's line of work leaves no room for error, as people's lives could depend on the reliability of a design.
Case Study
Revolutionizing Schematic Entry: A Case Study on Simulation Technologies, Inc. and Altium Designer
Simulation Technologies, Inc. (SimTech), a developer and manufacturer of advanced simulations for US military programs, was facing a significant challenge with its existing Electronic Design Automation (EDA) tool. The tool, which had been in use for approximately twenty years, was no longer capable of meeting SimTech’s Printed Circuit Board (PCB) needs due to declining product support and infrequent, insignificant upgrades. The company was under increasing market pressure to deliver smaller, more powerful technologies faster. SimTech needed a more sophisticated toolset that could deliver quick turnaround, comprehensive documentation, and parts management. However, as a supplier of military equipment, SimTech could not afford extensive downtime associated with toolset change. The new system had to be learned quickly, competently, and without error to maintain product integrity.
Case Study
BAE Systems Australia Leverages Altium Designer for Advanced HF Radar Technology
Monitoring Australia’s vast northern coastline is a crucial part of the country's national security program. However, the enormous area involved presents the challenge of detecting objects beyond the horizon. The Australian Defence Force’s (ADF) Jindalee Over The Horizon Radar (OTHR) system, near Alice Springs in central Australia, overcomes the normal range limitations caused by the earth's curvature by bouncing signals off the ionosphere using a series of antennas that stretch over 3.4 kilometres. BAE Systems Australia, a leading global defence company, supports the ongoing development of the super-sensitive Jindalee radar with advanced receiver and signal processing systems that help to extend the capabilities of the ADF’s Jindalee Operational Radar Network (JORN). However, creating these systems requires BAE Systems to remain at the cutting edge of HF radar technology, including the development of RF and high-speed data processing systems. Typical HF projects require up to 10-layer FR4 boards that comply with strict performance goals in both the analog and digital domain, necessitating advanced tools and design systems for the successful development of the OTHR subsystems.
Case Study
Nuvation Engineering: Accelerating Design Services with Altium Designer
Nuvation Engineering, one of the largest independent electronic design services companies in North America, offers a wide range of design services to a diverse customer base. The company's engineering process must be predictable and repeatable to meet customers' requirements within agreed timeframes. The company has developed a set of 'best-of-breed' processes and methodologies to achieve consistently short design times. However, to enable the 'right first time' design ethos, Nuvation has in place a strong peer design review process. This process requires the company to have the best designers, tools, and methodologies that allow them to control and predict the process. The challenge was to improve its hardware development cycles and find a tool that was quick to learn, easy to use, efficient, and had IP core design re-use.
Case Study
Delkin Devices Enhances Productivity with Altium Designer Upgrade
Delkin Devices, a leading manufacturer of industrial storage products, had been using Altium Designer 2004 for five years. However, as electronics design evolved, the software was no longer meeting their design needs. The team at Delkin Devices recognized the need for an upgrade to keep up with the changing demands of their industry. The challenge was to find a solution that would not only meet their current needs but also provide a platform for future growth and development. The solution needed to be easy to implement, with a minimal learning curve, and be able to handle their existing project files.
Case Study
Revitalizing Iconic Audio Systems with IoT: A Case Study on Linn Products
Linn Products, a company renowned for its high-end audio systems, faced a significant challenge when it decided to update its flagship product, the Sondek LP12 turntable, which was originally developed in 1972. The company needed to incorporate a new phono stage, named Eureka, into the LP12, a task that seemed almost impossible given the constraints of the turntable's design. The aesthetics of the audio systems were also crucial for Linn Products, requiring the electronics to be as visually appealing as the external casings. Prior to this, Linn Products had been using a series of disparate tools for its electronic designs, which resulted in a lack of clear link between the schematic and the board layout. This led to engineers spending more time maintaining the tool than being creative, which was not conducive to the company's philosophy of 'music for life'.
Case Study
Danish Interpretation Systems: Pioneering Digital Conferencing with Altium Designer
Danish Interpretation Systems (DIS), a company with over 50 years of experience in the communications and meeting industry, was faced with the challenge of developing the world’s first fully-digital conferencing system, the DCS 6000. The system was to handle the complexity of multi-language translations in real-time, with the ability to deliver 32 different language channels simultaneously and have eight active microphones in use at the same time. The system also needed to be fully expandable using LAN-based extension units. The design of the product was also a challenge as it had to be small enough to fit into the armrests of chairs or the legs of tables. The DCS 6000 required a high degree of design customization and power in the smallest possible enclosure.
Case Study
Esterline: Streamlining Aerospace and Military System Design with IoT Integration
Esterline Control Systems, Mason (ECS, Mason) is a company that develops flight controllers and other products for aerospace and military applications. These products are typically produced in small lots, such as 200 helicopters or 300 airplanes, which makes a full-custom design approach unfeasible. Instead, engineers modify existing standard product configurations to meet the needs of each customer. This process involves extensive iteration on the design, with design data being passed among teams and tools to meet the application's constraints. However, the company's original electrical design suite, based on OrCAD workstations, was inefficient. Importing and exporting design files to simulation, 3D modeling, and other analysis tools required a manual process that was slow and error-prone. The lack of integrated simulation and program management tools also hampered design and discouraged the exploration of design alternatives.
Case Study
Altium Designer Enhances Satellite Design Productivity at Penn State University
The Student Space Programs Laboratory (SSPL) at Pennsylvania State University provides undergraduate and graduate students with the opportunity to design, fabricate, and integrate real, working space systems. However, the design tool suite they were using, OrCAD, was proving to be a challenge. The system was slow and difficult to use, particularly for incoming undergraduates who were new to the field. The long learning curve and non-intuitive workflow resulted in frequent errors that had to be caught and corrected by more senior engineers. This was particularly problematic for the OSIRIS-3U CubeSat mission, a complex project that required system-level, electrical, and mechanical design efforts to create a compact satellite for studying space weather. The project was guided by three grad students and nearly 70 undergraduates, and the usability challenges of the design software were a significant obstacle to its completion.
Case Study
Vendo's Innovative Leap: From Traditional Vending Machines to Robotic Ones with Altium Designer
Sanden Vendo America Inc., a Dallas-based company with over 60 years of experience in the design, manufacture, and sales of vending equipment, decided to take their business to the next level by incorporating electronic control in their vending machines. Three years ago, the company decided to move the electronic design part of its operation in-house, through the purchase of suitable schematic entry and PCB layout software. This decision was aimed at achieving faster design turn-around time, increased IP security, and tighter design control. However, this move also presented potential challenges such as the software’s learning curve, efficiency, and quality of technical support. To maintain its leading position in the vending machine industry, Sanden Vendo needed electronic design tools that would facilitate its innovative designs without introducing production delays or compromises in quality control.
Case Study
Agilent-Qianfeng Electronics Technologies: Accelerating R&D with IoT
Agilent-Qianfeng Electronics Technologies, a joint venture between Agilent Technologies and Chengdu Qianfeng Electronics, was established to tap into China's rapidly growing $200 billion electronics industry. The venture's R&D lab in Chengdu, Sichuan Province, needed highly productive electronics design software to produce valuable test and measurement (T&M) instrument research in the shortest possible time. The software's efficiency and quality were critical to achieving this goal, along with considerations such as cost and customer support. The lab was tasked with spearheading product R&D for the Agilent brand in the Chinese region, which required working to short development design cycles due to the local market's dynamic nature. The lab staff needed to become proficient in the development software tools quickly. While speed and efficiency were fundamental objectives, maintaining Agilent's reputation for accuracy and high reliability in their test instruments was also paramount, placing high demands on the software's accuracy and performance during the R&D phase.
Case Study
CAS Tecnologia's Journey to Design Independence with Altium Designer
CAS Tecnologia, a company specializing in intelligent automation and telemetry technology, was heavily reliant on outsourcing for critical parts of their product design process. This dependence on another company was a significant hindrance to their financial success and future growth potential. To continue growing in their industry, it became necessary for CAS to bring all of their design processes in-house for complete control and independence. The challenge was to integrate an electronics design process into their existing mechanical workflow. They needed a tool that offered a high degree of control between the electrical and mechanical elements of a design to ensure a correct fit. The products they were developing for the management and distribution of electricity, water, and gas required a high degree of electrical complexity, necessitating a very specific set of requirements from EDA software.
Case Study
Streamlining ASIC Verification with Altium Designer: A Case Study on STMicroelectronics
STMicroelectronics, a global semiconductor manufacturer, designs ASICs that function as the brains inside the latest generations of hard-disk drives. A critical step in the ASIC production is testing and verification using a custom development board. Each ASIC needs its own development board, designed and manufactured in parallel with the chip. These boards connect the prototypes to the motherboard and the hard drive assembly so engineers can put the ASIC through its paces. Any delay in the production of the boards threatens the rollout of the chip, as well as the company's bottom line. Last year, STMicroelectronics produced 11 of these ASICs, each requiring its own custom development board for evaluation. Just two engineers were responsible for these boards, producing a new one nearly every month. The engineers had to manage parts library maintenance, schematic capture, simulation, system design, PCB layout, and generating manufacturing files. The hard drive assemblies are notoriously difficult for their odd mechanical clearance rules, adding an extra layer of complexity to the process.
Case Study
Cornet Technology's Advanced Network Switching Systems: A Case Study
Cornet Technology, a leading supplier of physical layer switching products for networks systems worldwide, faced a significant challenge in maintaining its industry-leading position. The company's extensive array of data switching and processing products required a high level of expertise from both Cornet’s engineers and the development tools they used. The typical boards designed by Cornet were large, involving 12 layers and around 2000 components with controlled impedance requirements and a high degree of circuit area duplication. The design times were short, typically two to three weeks, yet the final performance and reliability of the product - and therefore the PCB - had to be first rate. Cornet’s extensible designs demanded a high degree of flexibility from the development software, which also needed to produce concept-to-reality board designs within the short production times required to fulfill key contracts and meet market demands.
Case Study
TVonics: Differentiating in the Digital TV Market through Altium Designer
TVonics, a UK-based manufacturer of digital TV set-top boxes, was looking to differentiate itself in a highly competitive market. The company aimed to offer stylish, sleek, and energy-efficient products, which required strict design criteria at the board level, particularly for form factor and power consumption. The products also needed to offer class-leading signal reception and be designed for cost-effective manufacture. Furthermore, the company set itself challenging development time scales. For instance, the MDR-200 Digital TV Receiver, a significant redesign of an existing product, was expected to go from drawing board to manufacture in just four months. As a startup with a small design team and limited resources, TVonics was in search of a cost-effective design tool that was easy to use and came with good UK support.
Case Study
Omnisys Instruments: Managing Design Revisions and Component Lifecycles with Altium
Omnisys Instruments, a Swedish SME specializing in the development and production of complex, high-performance hardware products for the space industry, faced significant challenges in managing design revisions and component lifecycles. The company was involved in the sequential development of several major projects for Europe’s scientific and space industry, which incorporated advanced analog, microwave, ASIC, and power electronics. The extreme conditions found beyond Earth’s atmosphere amplified the normal constraints of electronics design, necessitating careful component selection and rigorous testing of designs to ensure high reliability after deployment. It was crucial for Omnisys to ensure that only approved components were used and thoroughly prototyped and tested designs were released to manufacture.
Case Study
Engineering Celebrity Joe Grand's Use of Altium Designer for Rapid Electronics Design in TV Show
Joe Grand, a renowned computer engineer and founder of Grand Idea Studio, was approached by the Discovery Channel in 2008 to co-host and engineer a new show, Prototype This. The show involved a team of engineers creating unique and novel prototypes for each episode, requiring skills in mechanics, electronics, materials science, and software engineering. However, the production schedules and timelines of the TV show often trumped the more thoughtful engineering processes required to design and build complex products. Most episodes were allotted only two weeks from concept to finale, with much of the team’s time spent in front of cameras, traveling, or doing interviews. As a result, Joe typically had just a few days to complete the electronics portion of the project, going from hand-built breadboard to final-ready circuit board in a matter of days.
Case Study
Revolutionizing Product Design: Full Gauge Controls' Transition to Altium Designer
Full Gauge Controls, a company that develops and produces digital instruments for control and indication of temperature, humidity, time, pressure, and voltage, was facing challenges with its old development process. The process was heavily dependent on prototype-based design verification, which was putting pressure on the design schedule and the design team. The traditional process involved sending a completed PCB design to a prototype manufacturer, which took approximately seven days for preparation of purchase order, production, and shipping. This process was not only costly but also often required additional prototypes for further design cycles and tests. In 2007, the company attempted to speed up the process by acquiring a rapid prototyping machine. However, the prototype boards still had to be manually assembled, which was inefficient and prone to rework. Moreover, the company had to bear the cost of maintaining the machine, which included high prices and time delay of replacement parts shipped from outside the country.
Case Study
Spectrum Integrity: Enhancing RF and Ultra-High-Speed Digital Design with Altium Designer
Spectrum Integrity, a company that designs ultra-high-speed digital, RF, and microwave PCBs, faced significant challenges in its design process. The company's unique design requirements necessitated a proprietary process, but it also had to interface with industry-standard component libraries and the design review processes of its clients. The company relied on a collection of specialized tools, but the native schematic capabilities in these tools were unusable. Instead, Spectrum Integrity had to use a third-party schematic tool that prevented synchronization of layout and schematic and lacked cross-probing capability. This made the process disjointed. Additionally, there was no free external viewer feature for the board designs, and no simple way to export design files. The frequent client reviews were a tedious and long process. The company had tried to streamline the process using PADS, but its schematic capture tool was similarly inadequate, and its version control was missing critical built-in functionality.
Case Study
Digital Design Corporation: Overcoming Design Challenges with Altium Designer
Digital Design Corporation (DDC) faced a complex challenge in designing a system capable of recording, processing, and analyzing video image data. The design requirements were demanding, including the need to withstand extreme temperatures and environments typical of military and rugged industrial applications. The system also had to cope with noisy power supplies, high G-forces, and vibration, all within a compact size. The design process required close collaboration among various disciplines, including system, schematic, board, mechanical, chip, firmware, and software design. The high frequencies involved in modern digital designs necessitated a broad experience base and high-powered tools. DDC's Video and Advanced Data Recorder (VAADR) was designed for military avionics applications, with most of its functionality residing on one controller board that interfaces with removable storage modules. The large sizes of the FPGAs used in the design presented a significant board design and layout challenge.
Case Study
Revamping Precision Agriculture: Leica Geosystems' Journey with Altium Designer
Leica Geosystems, a company known for its precision farming applications, faced a significant challenge during the development of the Leica mojoRTK, an auto-steer guidance system. The company had outsourced one of its boards to a contractor, a decision that soon proved to be a mistake. The board was returned behind schedule and failed to meet any of its design and manufacturing requirements. This left Leica Geosystems with a defunct PCB and a looming product launch. The company was faced with a critical decision: risk going back to the contractor, or overhaul the design and complete it in-house. The latter option was not going to be easy as the engineers needed to recapture the board design, translate files, and carefully recreate the PCB.
Similar Suppliers.
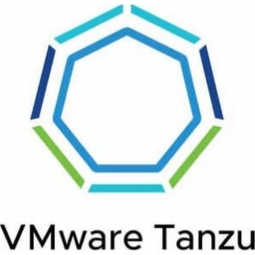
Supplier
VMware Tanzu (Dell Technologies)
VMware is a software company providing cloud and virtualization services that powers complex digital infrastructure. The company accelerates digital transformation by enabling unprecedented freedom and flexibility in how its customers build and evolve IT environments. Its software helps business users simply and securely access the apps and data they need, from anywhere, to do their best work. The company's software spans compute, cloud, networking and security, and digital workspace.
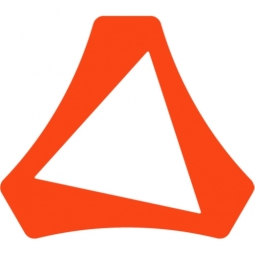
Supplier
Altair
Altair is a leading provider of enterprise-class engineering software enabling innovation, reduced development times, and lower costs through the entire product lifecycle from concept design to in-service operation. Our simulation-driven approach to innovation is powered by our integrated suite of software which optimizes design performance across multiple disciplines encompassing structures, motion, fluids, thermal management, electromagnetics, system modeling and embedded systems, while also providing data analytics and true-to-life visualization and rendering.
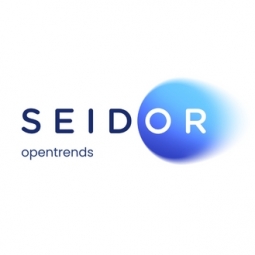
Supplier
Opentrends
Opentrends provides the most advanced custom software solutions to place companies in the Digital Transformation path, allowing them to achieve innovation advantage and contribute to their growth acceleration.More than 18 years delivering innovative projects of high technological complexity in a wide range of industries, while guaranteeing quality and alignment with our client’s objectives. In fact, over a hundred global companies across various industries have full Trust in our unique ability to design, build, implement, and integrate complex software innovations into their organizations.Let’s excel your digital future today.
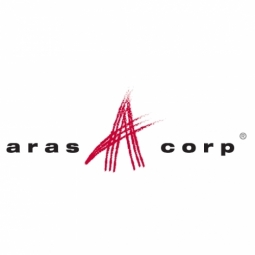
Supplier
Aras Corp
Aras Corp is a leading provider of product lifecycle management and digital thread solutions. Its extensive out-of-the-box functionality and modern web-based, cloud-ready architecture enable you to deploy quickly and continuously enhance your PLM environment in a fraction of the time required by conventional enterprise PLM / PDM systems and at a total cost of ownership far below that of any leading competitor.
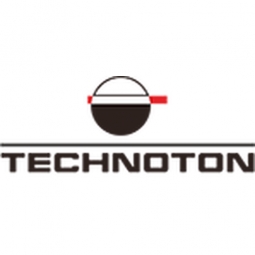
Supplier
Technoton
We offer comprehensive solutions for remote monitoring of road and off-road trucks, locomotives, sea and river vessels, diesel generators (gensets), fuel storages and tanks, technological machines. Major parameters monitored are: fuel consumption, time and engine operation mode, volume and temperature of fuel, operation of attached equipment, axle load.