技术
- 功能应用 - 计算机化维护管理系统 (CMMS)
- 机器人 - 轮式机器人
适用行业
- 设备与机械
- 可再生能源
适用功能
- 维护
- 仓库和库存管理
用例
- 实时定位系统 (RTLS)
- 资产跟踪
服务
- 系统集成
关于客户
NARENCO 成立于 2009 年,是一家可再生能源公司,致力于设计、开发、建造和运营公用事业规模的太阳能装置。他们的太阳能发电厂占地约 60 至 650 英亩,每个站点发电量高达 70 兆瓦。 NARENCO 监督每个太阳能项目的每个阶段——从场地开发到运营和维护。他们管理安装在 36 个客户站点的 4,000 多个资产。 NARENCO 的维护、可靠性和运营团队严重依赖计算机化维护管理系统 (CMMS) 软件。
挑战
NARENCO 是一家可再生能源公司,设计、开发、建造和运营公用事业规模的太阳能装置。他们管理安装在 36 个客户站点的 4,000 多个资产。然而,他们之前的计算机化维护管理系统(CMMS)限制太多,无法适应他们的需求。这导致了他们的技术人员的抵制,他们已经在以前的系统中遇到过故障。另一个挑战是维护操作的复杂性和独特性。 NARENCO 运营和维护 36 个太阳能站点,但并不拥有所有这些站点。这在合同、报告、库存等方面带来了复杂性。因此,他们需要一个高度可配置的 CMMS 来满足他们的独特需求。
解决方案
NARENCO 改用 eMaint,这是一种高度可配置的 CMMS,它提供了开箱即用功能和高水平可定制性的完美平衡。实施过程于 2021 年 10 月开始,目标是在 12 月向团队推出。该团队使用了各种工具和资源,包括 eMaint University、eMaint 的客户成功门户以及持续的内部培训,在整个实施过程中准备和培训员工。该实施使 NARENCO 能够立即开始使用 eMaint,同时还根据自己的需求定制平台。 eMaint 的移动 CMMS 功能对于 NARENCO 来说也是一个重要优势,允许他们的技术人员从任何地方完成任务、进行工单收费、添加文档、更新注释等。
运营影响
数量效益
Case Study missing?
Start adding your own!
Register with your work email and create a new case study profile for your business.
相关案例.
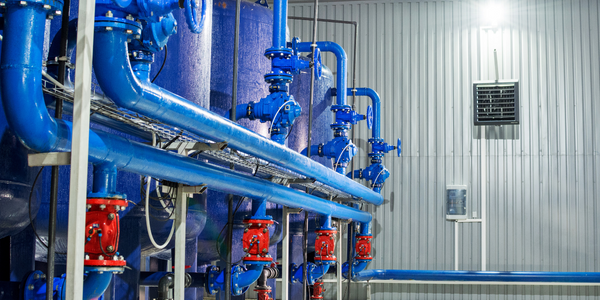
Case Study
Smart Water Filtration Systems
Before working with Ayla Networks, Ozner was already using cloud connectivity to identify and solve water-filtration system malfunctions as well as to monitor filter cartridges for replacements.But, in June 2015, Ozner executives talked with Ayla about how the company might further improve its water systems with IoT technology. They liked what they heard from Ayla, but the executives needed to be sure that Ayla’s Agile IoT Platform provided the security and reliability Ozner required.
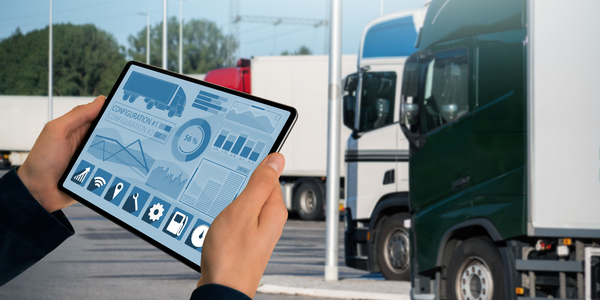
Case Study
IoT enabled Fleet Management with MindSphere
In view of growing competition, Gämmerler had a strong need to remain competitive via process optimization, reliability and gentle handling of printed products, even at highest press speeds. In addition, a digitalization initiative also included developing a key differentiation via data-driven services offers.

Case Study
Remote Monitoring & Predictive Maintenance App for a Solar Energy System
The maintenance & tracking of various modules was an overhead for the customer due to the huge labor costs involved. Being an advanced solar solutions provider, they wanted to ensure early detection of issues and provide the best-in-class customer experience. Hence they wanted to automate the whole process.
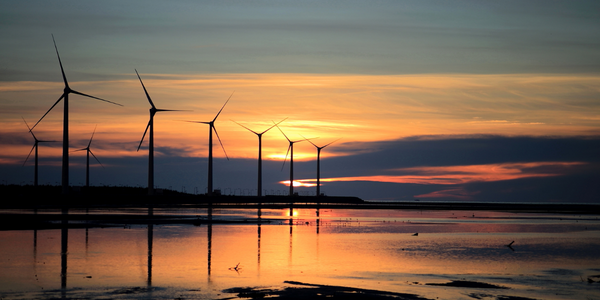
Case Study
Vestas: Turning Climate into Capital with Big Data
Making wind a reliable source of energy depends greatly on the placement of the wind turbines used to produce electricity. Turbulence is a significant factor as it strains turbine components, making them more likely to fail. Vestas wanted to pinpoint the optimal location for wind turbines to maximize power generation and reduce energy costs.
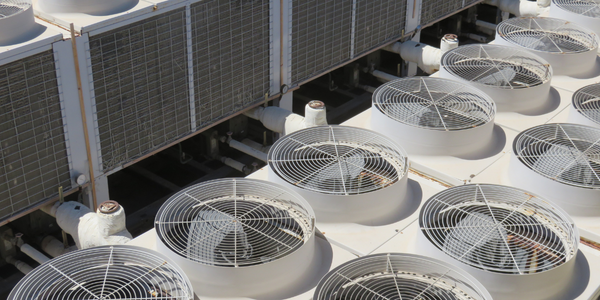
Case Study
Predictive Maintenance for Industrial Chillers
For global leaders in the industrial chiller manufacturing, reliability of the entire production process is of the utmost importance. Chillers are refrigeration systems that produce ice water to provide cooling for a process or industrial application. One of those leaders sought a way to respond to asset performance issues, even before they occur. The intelligence to guarantee maximum reliability of cooling devices is embedded (pre-alarming). A pre-alarming phase means that the cooling device still works, but symptoms may appear, telling manufacturers that a failure is likely to occur in the near future. Chillers who are not internet connected at that moment, provide little insight in this pre-alarming phase.
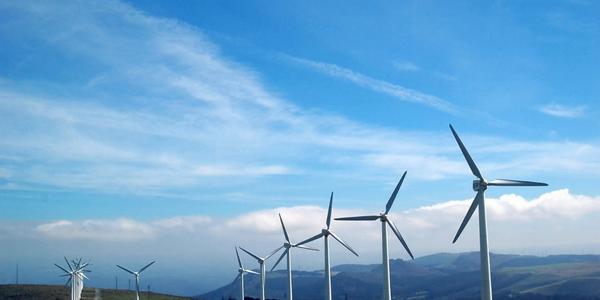
Case Study
Siemens Wind Power
Wind provides clean, renewable energy. The core concept is simple: wind turbines spin blades to generate power. However, today's systems are anything but simple. Modern wind turbines have blades that sweep a 120 meter circle, cost more than 1 million dollars and generate multiple megawatts of power. Each turbine may include up to 1,000 sensors and actuators – integrating strain gages, bearing monitors and power conditioning technology. The turbine can control blade speed and power generation by altering the blade pitch and power extraction. Controlling the turbine is a sophisticated job requiring many cooperating processors closing high-speed loops and implementing intelligent monitoring and optimization algorithms. But the real challenge is integrating these turbines so that they work together. A wind farm may include hundreds of turbines. They are often installed in difficult-to-access locations at sea. The farm must implement a fundamentally and truly distributed control system. Like all power systems, the goal of the farm is to match generation to load. A farm with hundreds of turbines must optimize that load by balancing the loading and generation across a wide geography. Wind, of course, is dynamic. Almost every picture of a wind farm shows a calm sea and a setting sun. But things get challenging when a storm goes through the wind farm. In a storm, the control system must decide how to take energy out of gusts to generate constant power. It must intelligently balance load across many turbines. And a critical consideration is the loading and potential damage to a half-billion-dollar installed asset. This is no environment for a slow or undependable control system. Reliability and performance are crucial.