技术
- 应用基础设施与中间件 - 事件驱动型应用
- 传感器 - 自动驾驶传感器
适用行业
- 汽车
- 医疗保健和医院
适用功能
- 销售与市场营销
用例
- 时间敏感网络
- 基于使用的保险
关于客户
OEConnection 是汽车行业数据、软件和服务的领先提供商,帮助推动 OEM 零部件销售。该公司拥有一支强大的客户成功团队,在北美拥有 20 多名代表,每名代表管理着 500 至 1,000 名经销商。该团队分为不同的领域和职能,入职代表帮助新客户熟悉产品和服务,优化代表(或客户经理)管理客户健康和产品使用情况,以推动更好的结果。
挑战
OEConnection 是一家为汽车行业提供数据、软件和服务的提供商,在扩大客户成功团队和提高客户参与度方面面临着挑战。该公司在北美有 20 多名客户代表,每个代表管理着 500 到 1,000 名经销商。客户参与的主要方法是电子邮件和电话,事实证明这非常耗时,而且经常被客户忽视。该公司根据使用情况将客户分为三组,每组的推广策略都不同。然而,这种手动外展不仅是劳动密集型的,而且还导致参与度低,尤其是那些最需要关注的客户。
解决方案
为了应对这些挑战,OEConnection 实施了 Conversica AI Assistants 以实现客户成功。自 2018 年 1 月以来,该公司一直在其销售团队中使用 Conversica 的对话式 AI,并决定利用它来扩大覆盖范围并提高客户参与度。名为 Jenna Grant 的人工智能助手可用于多种目的,例如安排与客户的审核、解决使用率低的问题、接触有风险的客户、提醒客户使用某些功能以及与有取消风险的客户进行沟通。该解决方案使 OEConnection 无需雇用任何新员工即可管理其客户数量。人工智能助手代表团队向数千家经销商发送个性化电子邮件,使客户代表能够进行更富有成效的对话,并花更多时间促进客户健康。
运营影响
数量效益
Case Study missing?
Start adding your own!
Register with your work email and create a new case study profile for your business.
相关案例.
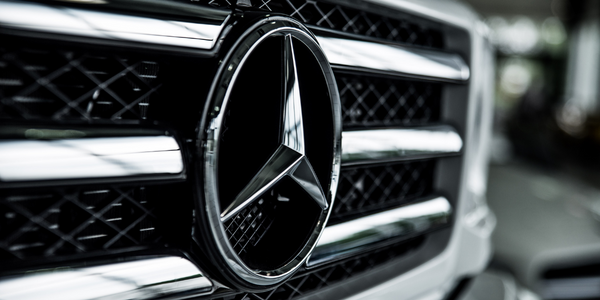
Case Study
Integral Plant Maintenance
Mercedes-Benz and his partner GAZ chose Siemens to be its maintenance partner at a new engine plant in Yaroslavl, Russia. The new plant offers a capacity to manufacture diesel engines for the Russian market, for locally produced Sprinter Classic. In addition to engines for the local market, the Yaroslavl plant will also produce spare parts. Mercedes-Benz Russia and his partner needed a service partner in order to ensure the operation of these lines in a maintenance partnership arrangement. The challenges included coordinating the entire maintenance management operation, in particular inspections, corrective and predictive maintenance activities, and the optimizing spare parts management. Siemens developed a customized maintenance solution that includes all electronic and mechanical maintenance activities (Integral Plant Maintenance).
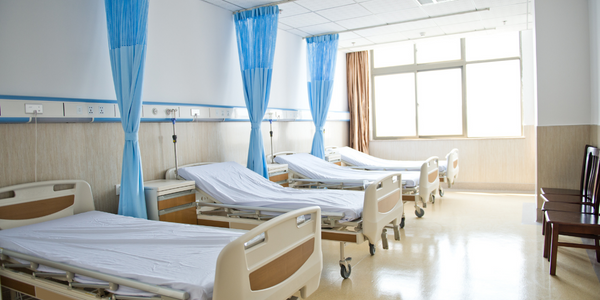
Case Study
Hospital Inventory Management
The hospital supply chain team is responsible for ensuring that the right medical supplies are readily available to clinicians when and where needed, and to do so in the most efficient manner possible. However, many of the systems and processes in use at the cancer center for supply chain management were not best suited to support these goals. Barcoding technology, a commonly used method for inventory management of medical supplies, is labor intensive, time consuming, does not provide real-time visibility into inventory levels and can be prone to error. Consequently, the lack of accurate and real-time visibility into inventory levels across multiple supply rooms in multiple hospital facilities creates additional inefficiency in the system causing over-ordering, hoarding, and wasted supplies. Other sources of waste and cost were also identified as candidates for improvement. Existing systems and processes did not provide adequate security for high-cost inventory within the hospital, which was another driver of cost. A lack of visibility into expiration dates for supplies resulted in supplies being wasted due to past expiry dates. Storage of supplies was also a key consideration given the location of the cancer center’s facilities in a dense urban setting, where space is always at a premium. In order to address the challenges outlined above, the hospital sought a solution that would provide real-time inventory information with high levels of accuracy, reduce the level of manual effort required and enable data driven decision making to ensure that the right supplies were readily available to clinicians in the right location at the right time.