公司规模
Large Corporate
地区
- Europe
国家
- United Kingdom
产品
- DocuWare
技术栈
- CRM system
- Accounting system
实施规模
- Enterprise-wide Deployment
影响指标
- Cost Savings
- Customer Satisfaction
- Productivity Improvements
技术
- 应用基础设施与中间件 - 数据交换与集成
适用功能
- 人力资源
- 采购
用例
- 库存管理
- 远程协作
服务
- 系统集成
- 软件设计与工程服务
关于客户
林地信托基金会成立于 1972 年,是英国最大的林地保护慈善机构,也是保护森林和树木的主要力量之一。该组织致力于保护古老森林、修复受损森林,并为受到开发威胁的森林而战。在社区、学校、组织和个人的帮助下,他们在英格兰、威尔士、北爱尔兰和苏格兰各地开辟了新的原生林地。该组织正在寻找一种解决方案,以法院合法接受的格式将其法律文件数字化,并安全地存储这些文件,保留期限长或无限。他们还需要一种可以与其他关键系统(如 CRM 和会计系统)集成的解决方案,并为在家办公的员工提供轻松访问重要信息的机会。由于近 2/3 的员工在家办公,因此通过平板电脑、智能手机或笔记本电脑通过互联网访问信息是一个重要的考虑因素。
挑战
英国林地保护慈善机构 Woodland Trust 面临的挑战是如何以法院合法接受的格式管理和存储其法律文件。他们还在寻找一种可以与其 CRM 和会计系统集成的解决方案,并为在家办公的员工提供轻松访问重要信息的机会。该组织计划搬到一座新的、更现代化的大楼,他们预计那里的存储空间会更少,这促使他们开始评估文档管理解决方案。任务包括减少存储空间、创建“合法可接受的”电子文档档案、与在家办公的员工共享信息,以及将文档管理系统与组织的 CRM 和会计系统集成。
解决方案
Woodland Trust 决定实施 DocuWare,因为它符合法院的法律要求,可以帮助他们减少文档存储空间,并可以根据他们的独特需求进行定制。DocuWare 最初被推广到法律部门,用于管理和存储土地征用文件和遗留文件,其中包含个人在其去世后将其部分遗产捐赠给 Woodland Trust 的详细信息。该组织扩大了 DocuWare 的用途,包括直接借记授权和礼品援助声明。使用定制的内部软件编程,DocuWare 与慈善机构的 CRM 系统 Advanced、NG 集成。一旦在 CRM 系统中找到捐赠者,就可以通过单击集成的 DocuWare 按钮来访问与该捐赠者相关的每个文档,该按钮在后台运行,自动搜索并显示使用捐赠者的参考编号索引的任何文档。
运营影响
数量效益
Case Study missing?
Start adding your own!
Register with your work email and create a new case study profile for your business.
相关案例.
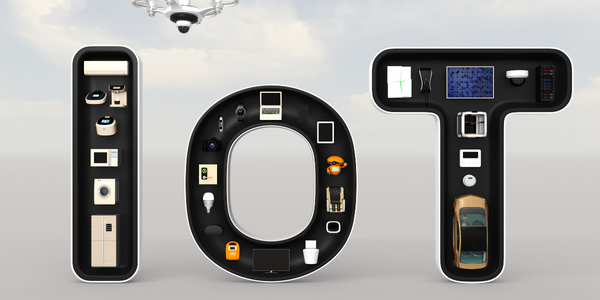
Case Study
Premium Appliance Producer Innovates with Internet of Everything
Sub-Zero faced the largest product launch in the company’s history:It wanted to launch 60 new products as scheduled while simultaneously opening a new “greenfield” production facility, yet still adhering to stringent quality requirements and manage issues from new supply-chain partners. A the same time, it wanted to increase staff productivity time and collaboration while reducing travel and costs.
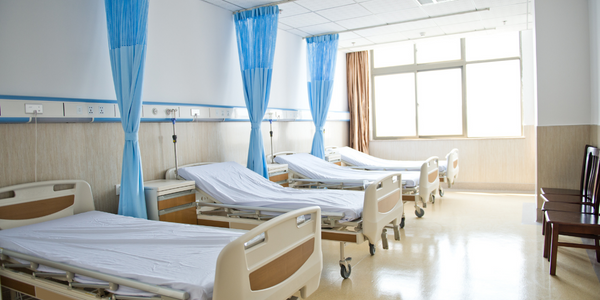
Case Study
Hospital Inventory Management
The hospital supply chain team is responsible for ensuring that the right medical supplies are readily available to clinicians when and where needed, and to do so in the most efficient manner possible. However, many of the systems and processes in use at the cancer center for supply chain management were not best suited to support these goals. Barcoding technology, a commonly used method for inventory management of medical supplies, is labor intensive, time consuming, does not provide real-time visibility into inventory levels and can be prone to error. Consequently, the lack of accurate and real-time visibility into inventory levels across multiple supply rooms in multiple hospital facilities creates additional inefficiency in the system causing over-ordering, hoarding, and wasted supplies. Other sources of waste and cost were also identified as candidates for improvement. Existing systems and processes did not provide adequate security for high-cost inventory within the hospital, which was another driver of cost. A lack of visibility into expiration dates for supplies resulted in supplies being wasted due to past expiry dates. Storage of supplies was also a key consideration given the location of the cancer center’s facilities in a dense urban setting, where space is always at a premium. In order to address the challenges outlined above, the hospital sought a solution that would provide real-time inventory information with high levels of accuracy, reduce the level of manual effort required and enable data driven decision making to ensure that the right supplies were readily available to clinicians in the right location at the right time.
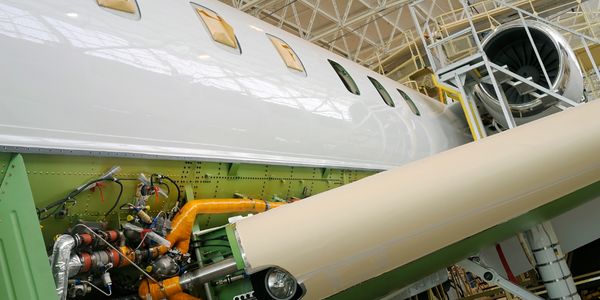
Case Study
Aerospace & Defense Case Study Airbus
For the development of its new wide-body aircraft, Airbus needed to ensure quality and consistency across all internal and external stakeholders. Airbus had many challenges including a very aggressive development schedule and the need to ramp up production quickly to satisfy their delivery commitments. The lack of communication extended design time and introduced errors that drove up costs.
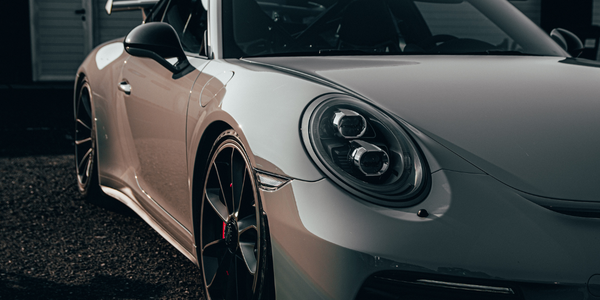
Case Study
Porsche Announces Augmented Reality at Scale, Powered by Atheer
The usual practice for car repairs at a Porsche car dealership is to have a factory representative or regional engineer visit to help diagnose the problem, and sometimes a faulty assembly is shipped back to company HQ for damage analysis. All that costs time and money for customers and dealers alike.