Everstream Analytics
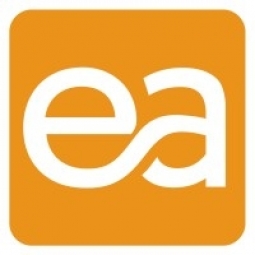
概述
总部
美国
|
成立年份
2012
|
公司类型
私营公司
|
收入
$10-100m
|
员工人数
201 - 1,000
|
网站
|
推特句柄
|
公司介绍
Everstream Analytics sets the global supply chain standard. Through the application of Artificial Intelligence and predictive analytics to its vast proprietary dataset, Everstream delivers the predictive insights and risk analytics businesses need for a smarter, more autonomous and sustainable supply chain. Everstream’s proven solution integrates with procurement, logistics and business continuity platforms generating the complete information, sharper analysis, and accurate predictions required to turn the supply chain into a business asset.
Supplier missing?
Start adding your own!
Register with your work email and create a new supplier profile for your business.
实例探究.
Case Study
Schneider Electric's Transformative Approach to Supply Chain Risk Management
Schneider Electric, a global provider of energy management and automation solutions, manages around 360,000 shipments annually across seven global regions. The company's customers expect their orders to be delivered on time, in full, and in perfect condition. To meet these expectations, Schneider Electric needed to improve the performance of its global supply chain. This required efficient networks, reliable processes, capable logistics partners, and a smart approach to risk management. The company needed to be able to respond rapidly to any delays or disruptions in the supply chain and reassure its customers that their critical equipment was on its way. Schneider Electric's pursuit of excellence led the company to embark on a comprehensive supply chain transformation with the goal of significant improvements in efficiency, visibility, and risk management.
Case Study
Google Data Center Logistics powered by Everstream Analytics
Google operates a vast network of facilities, including hyperscale data centers and smaller installations, to provide its sophisticated information services. The company designs and assembles much of the equipment used in these data centers in-house, which necessitates a complex physical supply chain. This supply chain handles everything from complete servers to components, racks, and networking equipment. Google manages hundreds of thousands of shipments annually between thousands of origin destinations. The cargo is often high-value, proprietary, and time-critical. The loss or delay of a single item can throw a build project off schedule and risk exposing sensitive intellectual property. Therefore, Google needed a solution to identify supply chain risks before they impact the in-transit supply chain.
Case Study
Mitigating Supply Chain Risk: A Case Study of DHL and ZF Partnership
ZF, a global leader in driveline and chassis technology as well as active and passive safety technology, was facing significant challenges in managing its supply chain risk. The company's scale and global scope, which involved delivering 35,000 parts weighing 4,000 tons to locations all over the world in 2013 alone, raised concerns about potential disruptions. Airfreight was considered a 'last resort' at ZF, used only when essential to maintain production schedules and avoid customer delivery delays. This made it a significant risk, especially if disruption occurred at a critical airport. ZF also identified inefficiencies in providing timely and accurate incident information to automotive OEMs detailing potential impact at supplier- and material number-levels. The company wanted to find ways to mitigate and effectively manage this risk to ensure business continuity in its end-to-end supply chain.
Case Study
Schmitz Cargobull Enhances Supply Chain Visibility with Everstream Analytics
Schmitz Cargobull AG, Europe’s leading manufacturer of semi-trailers and trailers, faced a significant challenge in managing its complex supply chain. The company, which produces over 45,000 vehicles annually and has a turnover of €1.6 billion, operates on a global scale with plants across Europe and Asia. Following rapid business growth and expansion into new geographies, Schmitz Cargobull needed better supply chain visibility and transparency on logistics flows, right down to component level. The company's trailer customers can typically change their order right up to the point of production, and some custom-built items must be urgently produced within 18 hours. The trailer subsector also features high demand volatility, requiring just-in-time and 100% make-to-order inbound supply chain processes. Schmitz Cargobull aimed to obtain a global yet detailed view of daily events, especially those impacting their own production sites or their global supplier base. They also wanted to improve efficiency and reduce logistics costs by building awareness and knowledge of Tier 1 suppliers and the outbound distribution network.
Case Study
Enhancing Supply Chain Resilience and Visibility: A Case Study on DuPont Electronics and Industrial
DuPont Electronics and Industrial (E&I), a global innovation leader with technology-based materials and solutions, was grappling with low resilience and supply chain agility. The company was also in need of more insights into production locations. The urgency to address these issues was driven by both customer needs and industry standards. DuPont E&I was seeking a solution that would not only strengthen their risk management organization but also build resiliency into their existing supply chain. The ideal solution would provide network visibility, identify potential risk points, and make customers feel comfortable and confident about the delivery of their products. The company also wanted to establish an open line of communication to meet customer needs, even during exceptions.
Case Study
Enhancing Supply Chain Resilience and Efficiency: A DuPont Case Study
DuPont, a global science and innovation company, faced significant challenges in managing its complex supply chain. The supply chain strategy was not defined by the logistics team, but by multiple business units within the organization, making it difficult to achieve a holistic view of the entire supply chain. DuPont's key objective was to assess risk and improve efficiency across its supply chain. The company had previously experienced damaging disruptions, including the 2011 tsunami in Japan that affected its sole supplier plant and the 2013 strikes in the U.S.A. that disrupted operations at East Coast ports. DuPont was seeking a solution that would provide visibility of different routes and specific modes of transport, along with both global and per-country perspectives.
Case Study
Evonik's Enhanced Risk Analysis and Improved Planning with IoT
Evonik Industries AG, a leading specialty chemicals company, has a critical need for risk management due to the nature of its operations. The company's services unit, Evonik Technology & Infrastructure GmbH, is responsible for managing site operations, utilities, waste, technical services, and logistics. The Logistics department manages the complete supply chain, including the receipt of raw material, warehousing, and the shipping of finished products. In 2015 alone, the company transported 5,531,000 tons of hazardous goods by air, sea, rail, or road. The company has its own transport risk analysis system, but it needed a more comprehensive solution to ensure the safety of all parties and supply chains involved. The transportation of hazardous goods needs to be well planned and monitored to minimize the impact of disturbances such as traffic jams or accidents on route. To keep risks under control, Evonik needed a full picture of the status of goods in transit and the ability to intervene with the best alternative solution if necessary.
Case Study
Glanbia's Innovative Approach to Protecting Temperature Sensitive Products
Glanbia PLC, a global nutrition group and leading cheese manufacturer, was facing a significant challenge in protecting its temperature-sensitive products during transit. The company's Performance Nutrition division (GPN), a major revenue generator, was experiencing growth in its portfolio and product offerings, necessitating the need for new technologies to ensure product safety. In 2019, the company was hit with rail embargos and supply chain disruptions, resulting in product loss. This, coupled with issues of product freezing in cold weather and melting during hotter months, sparked a need for change. The company's goal was to continue expanding by employing and using 3rd party logistics, including current partnerships with DHL and Transplace, while mitigating risks for temperature-sensitive shipments and decreasing product loss due to temperature fluctuations.
Case Study
Enhancing Security and Resiliency in High-Risk Regions with IoT: A Case Study of ANDRITZ and Everstream Analytics
ANDRITZ GROUP, a global supplier and servicer of complex, high-value plant equipment, faced significant challenges in ensuring the safety and security of its staff and worksites across 120 countries, including politically unstable regions like Central Africa and the Pakistan-Afghanistan border. The company needed to deliver equipment and materials securely to these sites and ensure that its personnel could conduct work safely. The responsibility of putting infrastructure and operating procedures in place to allow this fell on the company’s corporate security function. The security team at ANDRITZ relied on a multi-layered, intelligence-led risk assessment process, collecting information on historical incidents and emerging threats from a variety of data sources. However, with so many sites spread across the world, the team needed a more efficient and effective solution for risk assessment and incident monitoring.
Case Study
Cisco's Proactive Approach to Supply Chain Risk with Everstream Analytics
Cisco, a global IT leader, relies on DHL Service Logistics for managing a comprehensive service and support logistics operation across 19 countries in Asia-Pacific. The operation includes hardware and spare parts from 80 rapid DHL fulfillment sites operating 365 days a year. However, the network faced challenges in coping with unexpected events, ranging from minor transport delays to major natural disasters. The objective was to improve service operations performance and enhance the support provided to Cisco customers. The need was to enhance the network's resilience and agility to handle unexpected events effectively.
Case Study
Deutsche Post DHL's Single-Platform View of All Operations: A Case Study
Deutsche Post DHL Group (DPDHL), the world’s leading postal and logistics services group, faced a significant challenge in sharing security information in a timely manner across its vast network. The company's security network comprises 1,000 managers, 12,000 locations, and 485,000 employees in over 220 countries. The Corporate Security Department, which operates the Global Security Situation Center (GSSC), provides strategic direction and support, while security implementation and operations are managed at regional/country levels. The company faced risk events such as political instability, social unrest, and natural disasters that could threaten its operations, employees, and corporate assets. The efficiency of the GSSC was compromised due to the scale of the monitoring task and the proliferation of inputs from numerous databases, Excel files, email and telephone reports, and more. This high complexity made it possible for critical issues to be missed.
Case Study
SOS Children's Villages Enhances Disaster Response with IoT
SOS Children's Villages, a global organization working to safeguard children and protect their rights in some of the world's most challenging places, faced a significant challenge in ensuring the safety and security of its sites in 137 countries. Many of these locations are in the world's least stable and most vulnerable regions, often affected by natural and manmade disasters. The organization has a permanent Global Emergency Response (GER) Team, based in Austria, whose role is to monitor emerging risks, from severe weather events to political unrest, and deliver the appropriate support and resources to ensure the safety of its staff and beneficiaries on the ground. To accomplish its goals, the GER team needed access to timely, accurate, and detailed information.