Visual Knowledge Share Ltd
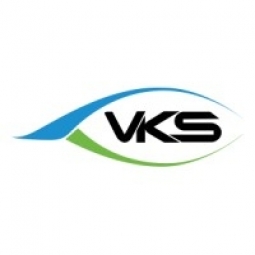
概述
公司介绍
Visual Knowledge Share Ltd. has created an innovative Electronic Work Instruction solution developed to empower the manufacturing workforce. This solution helps shop floor employees share knowledge and best practices through easy to use visual work instructions. Our software enables employees to improve their productivity, efficiency, and work quality, thereby giving them an increased feeling of accomplishment and satisfaction.
Supplier missing?
Start adding your own!
Register with your work email and create a new supplier profile for your business.
实例探究.
Case Study
Digitization and Process Improvement in Valve Manufacturing: A Case Study
Valve Research & Manufacturing Company, a manufacturer of valves for various applications, was facing challenges with its outdated paper-based system for assembly instructions. The company had to deal with the cumbersome process of printing and distributing assembly instructions and engineering drawings to each operator. The operators then had to interpret these instructions without any visual aids. Whenever a revision was needed, it resulted in a chaotic process of tracking down jobs across the facility to update the paperwork. This was particularly challenging given the high precision components involved in the assembly process. The company also had to deal with the task of implementing real-time adjustments, which was a monumental task given the multiple job orders involved in each change. The paper-based system also required operators to leave their workstations to log each operation they were performing, which was time-consuming.
Case Study
Mitsubishi Electric's Smart Factory Transformation with VKS Work Instructions
Mitsubishi Electric, a leading elevator manufacturer, faced a complex challenge when scaling up production for its new MOVE elevator system, designed specifically for the European market. The MOVE elevators were quite different from the standard Japanese model, requiring new assembly processes. The company needed to standardize these processes to ensure high-quality production and maintain its reputation for reliability. However, initial efforts to standardize the shop floor were burdensome for the experienced workers, who were more comfortable with their individual routines. Furthermore, the company lacked a reliable data capturing system that could provide valuable feedback for analysis. The challenge was to implement a system that could streamline the new step-by-step instructions for the MOVE models, capture data for analysis, and be easily accepted by the workforce.
Case Study
Cleveland State University Empowers Future Manufacturers with VKS
The manufacturing sector is facing a significant skills gap, with an expected 2.1 million unfilled jobs by 2030, costing trillions for the US alone. To address this, manufacturing companies are adopting smart manufacturing tools and work instruction software. However, the challenge extends beyond the industry to educational institutions, which need to prepare the next generation of workers for the modern manufacturing environment. Cleveland State University (CSU) is one such institution, aiming to train its engineering students on smart manufacturing tools and their applications. The challenge is to provide students with a comprehensive understanding of product design and manufacturing system design, and to prepare them to close the skills gap in their future companies.
Case Study
IMEG-VKS Partnership: A Case Study on Effective Manufacturing Work Instructions
Industrial Management and Engineering Group, LLC (IMEG), an engineering firm established in 2006, was in search of a software solution that could improve productivity, flexibility, safety, and efficiency for their clients. The ultimate goal was to enhance the competitiveness and profitability of their clients. However, finding a user-friendly digital work instruction solution that could also collect data at a relatively inexpensive cost and was easy to implement was a challenge. The global reality of worker shortages and supply chain disruptions further complicated the situation. The need for constant readjustments to account for assembly line discrepancies and the increasing adoption of Industry 4.0 best practices in manufacturing, which required a multifaceted approach to quality lean production, added to the complexity of the challenge.
Case Study
Digital Transformation in Sensor Technology: A Case Study on Dinel Schneider Electric and VKS
Dinel Schneider Electric, a leading manufacturer of sensor technology, was facing challenges with their traditional paper-based work instruction system. The paper instructions were hard to manage, quickly became outdated, and were not efficient for a rapidly evolving corporation. The heavy reliance on text-based instructions made it difficult for operators to quickly understand their tasks and responsibilities. The company was seeking a solution to enhance the quality of their products and the efficacy of their workforce. They needed a system that could keep up with the pace of their innovation and provide clear, up-to-date instructions to their operators.
Case Study
Kone's Digital Transformation: Boosting Productivity and Streamlining Operations
KONE Coal Valley, a leading manufacturer of elevators and escalators, faced two significant challenges before their digital transformation. Firstly, their work instructions were distributed on paper within multiple binders, making it difficult to update and keep track of the best and most current practices. Secondly, with a significant portion of their workforce set to retire in the coming years, they had to hire a new generation of workers who lacked the necessary experience. The company needed a solution that would enable them to transfer the knowledge and experience of their senior employees to their new hires before they retired. These challenges were not unique to KONE Coal Valley alone but are common issues that many modern manufacturers face daily.
Case Study
VKS Boosts Performance and Efficiency at Mobility Worldwide
Mobility Worldwide, a charity that builds carts for individuals with physical disabilities in resource-poor countries, faced significant challenges in scaling up its production. The organization aimed to double its capacity from 2000 to 4000 carts per year, but faced hurdles due to lack of standardization, absence of bills of materials, and a workforce made up entirely of volunteers unfamiliar with lean manufacturing. The Columbia site, which produces the majority of the carts, operates at only 50% utilization due to volunteers typically working 3-4 hours at a time. The organization also faced logistical challenges due to the rural locations where the carts are deployed, making it difficult to supply replacement parts. Quality assurance was another major issue, as without verification of proper builds, the charity was unable to meet the long-term needs of its recipients.
Case Study
Revolutionizing Quality Inspection: A Case Study on Republic Manufacturing
Republic Manufacturing, a leading producer of industrial blowers and vacuum pumps, was facing challenges in maintaining the highest levels of quality for their customers. Their inspection process was twofold, involving operators recording quality data and performing inspections during assembly, followed by Quality Control inspectors verifying the product once completed. This process, while ensuring quality, was time-consuming and complicated due to the use of paper-based inspection reports. The company was also struggling with training their workforce due to frequent product changes and variations. The traditional paper-based methods were not only inefficient but also prone to errors and loss of data.