Samsara
几分钟内部署的完整传感器解决方案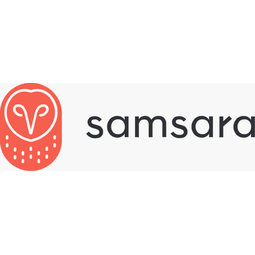
概述
总部
美国
|
成立年份
2015
|
公司类型
私营公司
|
收入
< $10m
|
员工人数
201 - 1,000
|
网站
|
推特句柄
|
公司介绍
Samsara 构建的传感器系统将无线传感器与远程网络和基于云的分析相结合——所有这些都在一个易于使用、以软件为中心的解决方案中。 Samsara 认为,通过使传感器易于部署和数据易于使用,客户将能够在以前从未使用过的地方部署数以千计的传感器。
物联网应用简介
Samsara 是平台即服务 (paas), 应用基础设施与中间件, 分析与建模, 功能应用, 网络与连接, 和 传感器等工业物联网科技方面的供应商。同时致力于建筑与基础设施, 和 运输等行业。
技术栈
Samsara的技术栈描绘了Samsara在平台即服务 (paas), 应用基础设施与中间件, 分析与建模, 功能应用, 网络与连接, 和 传感器等物联网技术方面的实践。
-
设备层
-
边缘层
-
云层
-
应用层
-
配套技术
技术能力:
无
弱
中等
强
Supplier missing?
Start adding your own!
Register with your work email and create a new supplier profile for your business.
实例探究.
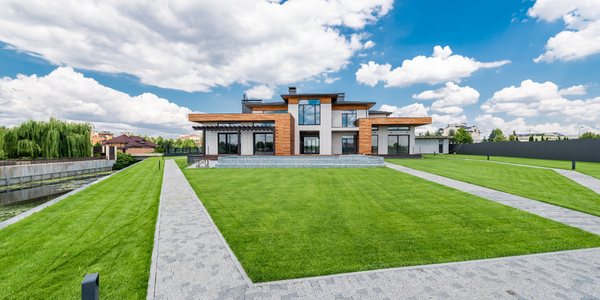
Case Study
Bellas Landscaping
Leading landscaping firm serving central Illinois streamlines operations with Samsara’s real-time fleet tracking solution: • 30+ vehicle fleet includes International Terrastar dump trucks and flatbeds, medium- and light-duty pickups from Ford and Chevrolet. Winter fleet includes of snow plows and salters.
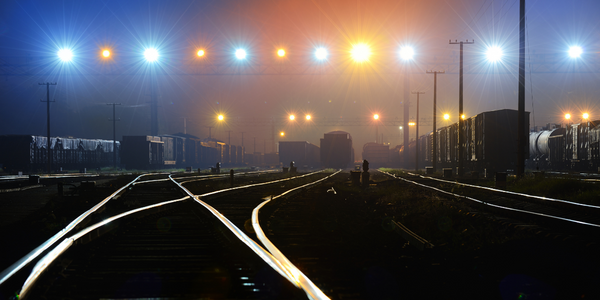
Case Study
How ITS ConGlobal Pioneered Fleet Electrification in their Industry
Needed a plan for investing in fleet electrification ITS ConGlobal (ITSC), one of the largest transportation support companies in the U.S., has long believed that it must operate sustainably—especially as the transportation and logistics industry is a leading source of CO2 emissions. Recent legislation aims to reduce greenhouse gasses (GHG) emissions from operations in the private sector. Still, ITSC has consistently invested in sustainable operations and stays well ahead of government-imposed regulations and timelines. In particular, they were interested in switching from diesel to electric vehicles (EVs). EVs are a significant investment of time and resources, especially considering the diverse needs of ITSC’s mixed fleet. They put together a systematic, data-driven plan for electrifying their fleet, starting with a pilot.
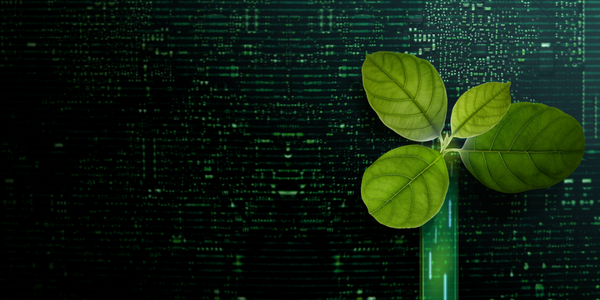
Case Study
Summit Materials: Enhancing Safety and Sustainability with IoT
Summit Materials, a leading integrated construction materials solution provider, was facing challenges in achieving their Environmental, Social, and Governance (ESG) goals due to decentralized solutions for telematics, safety, and site visibility. This decentralization led to gaps in their data and reporting, making it difficult to track progress against their goals. Their operations spanned across 22 U.S. states and British Columbia, Canada, further complicating the tracking process. Summit needed a technology partner that could consolidate their over the road fleet safety, emissions, and fuel consumption data into a single platform for better visibility and data reliability.
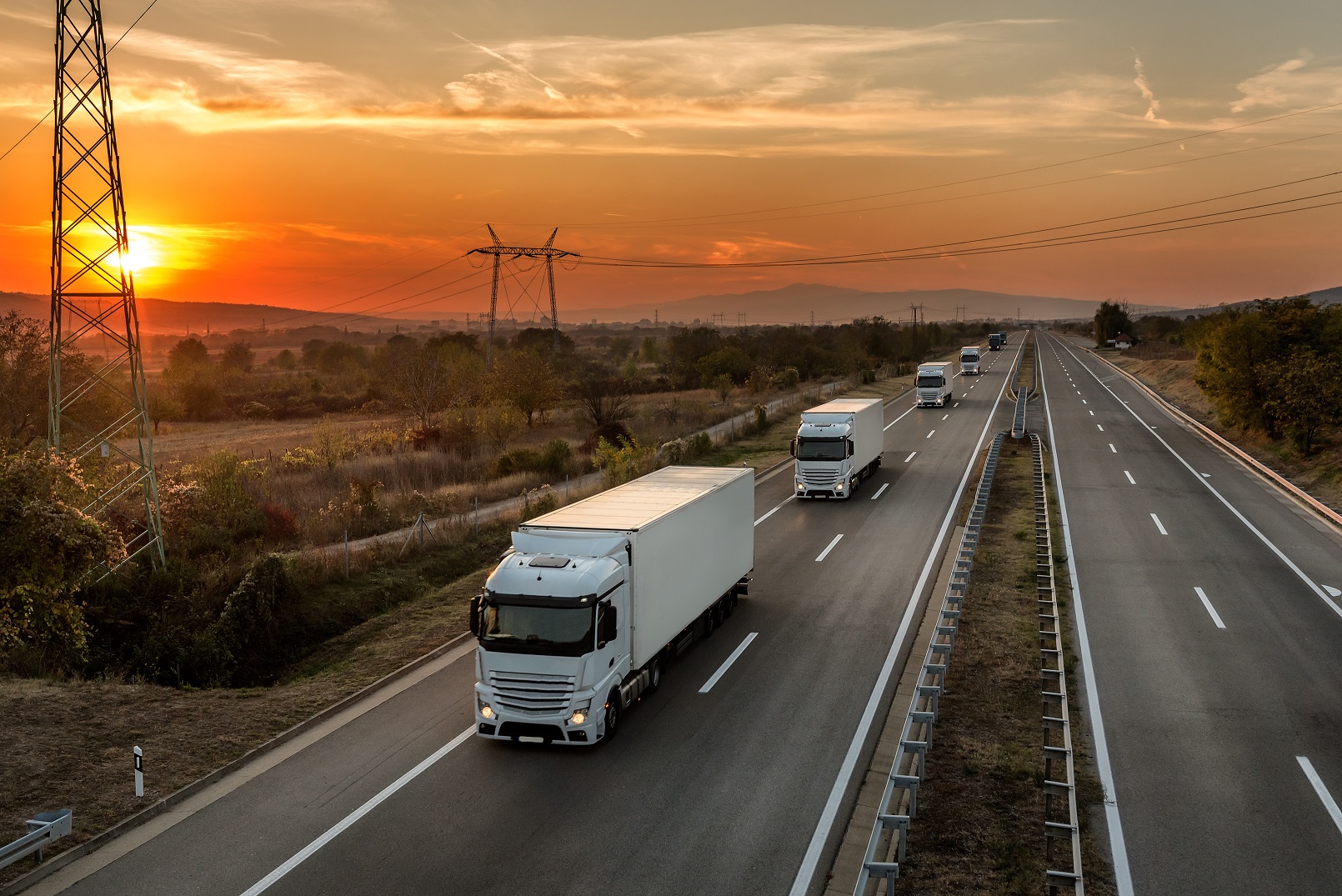
Case Study
Trasporti Romagna Enhances Operational Efficiency with Samsara's IoT Solution
Trasporti Romagna, an Italian logistics and transport company established in 1923, was seeking ways to increase the efficiency, security, and reliability of its fleet operations. The company aimed to expand its market share and strengthen its competitive edge. However, the legacy telematics system they were using was a significant obstacle. It offered poor visibility and usability, and lacked the integration of dash cams with the operations platform. This outdated system was hindering the company's ability to monitor and manage its fleet effectively, thereby affecting its overall operational efficiency and safety.
Case Study
SeniorCare EMS Enhances Fleet Safety and Efficiency with Samsara Solutions
Before implementing Samsara, SeniorCare EMS faced significant challenges in monitoring and improving driver safety. They had separate vendors for dash cams, GPS tracking, and wireless data, which made it difficult to consolidate and manage data effectively. The existing dash cams couldn't remotely upload footage, making it nearly impossible to monitor driver behavior in real-time. Additionally, the GPS tracking system provided location data at intervals of 30 seconds to a minute, which was insufficient for emergency response times. The company needed a more integrated and real-time solution to ensure driver safety, reduce risky driving behaviors, and improve operational efficiency.
Case Study
Summit Materials: Leveraging IoT for Enhanced Safety and Sustainability
Summit Materials, a leading integrated construction materials solution provider, faced challenges in achieving their Environmental, Social, and Governance (ESG) goals due to decentralized solutions for telematics, safety, and site visibility. This decentralization led to gaps in their data and reporting, hindering their progress towards their ambitious safety and sustainability goals. The company's vast operations, spanning 22 U.S. states and British Columbia, Canada, made it difficult to track progress against their goals. They needed a technology partner that could consolidate their over-the-road fleet safety, emissions, and fuel consumption data into a single platform, improving visibility across their distributed operations.
Case Study
BioTrans' Transformation: Enhancing Service and Reliability with IoT
BioTrans, a leading logistics service provider for the Laboratory Research transportation industry in North America, faced a significant challenge in maintaining the integrity of their temperature-sensitive cargo. The company transports research models that require precise temperature control throughout delivery, with a variance of just a few degrees potentially compromising the load. Each classification type also requires a specific temperature range, adding to the complexity of the logistical challenge. Prior to implementing Samsara, BioTrans' quality control team could only effectively monitor temperatures for eight hours per day when someone was on shift. During the remaining 16 hours, drivers would not receive out-of-range temperature alerts, leading to cargo loss that cost BioTrans anywhere between $2,000 to $20,000 and damaged customer relationships.
Case Study
How Heniff Reduces Driver & Onsite Incidents With Connected Video
Heniff Transportation, a bulk liquid transporter with over 1,800 drivers and 80 terminal locations, was facing significant safety challenges both on the road and at their worksites. The company was held liable for over half of the claims filed against it due to limited video visibility, which made it difficult to capture evidence of fraudulent incidents and protect drivers. At their terminal locations, workers often encountered slippery floors or extreme weather, leading to injury claims averaging $10,000 per incident. The company's legacy onsite security cameras provided limited visibility and required manually viewing every minute of footage to find and review an incident. Furthermore, their systems were siloed, making incident review inefficient for managers looking for a comprehensive understanding of events. When an incident did occur, it was difficult for Heniff to properly investigate and quickly retrieve video footage for a driving or onsite event.
Case Study
How a nearly 100-year-old agricultural supplier uses Samsara to improve safety, efficiency and customer satisfaction.
As Armstrong Richardson looked to continue its expansion and grow as a haulier, Steve Whitehead, National Transport Manager, knew he needed to find a more reliable fleet management solution. The company’s system at that time did not deliver as promised, often capturing inaccurate tracking data and losing video footage of accidents. During his demonstration by Samsara, Steve was immediately impressed by the all-in-one platform and accuracy of real-time GPS tracking in remote locations. After trialing the platform, it was an easy decision to move forward given Samsara’s reliability, ease of use and support. Today, Armstrong Richardson uses Samsara to improve customer service, increase safety and gain new insights into its fleet.
Case Study
Impossible Foods' Use of Samsara Sensors to Ensure Food Safety and Quality
Impossible Foods faced the challenge of scaling its production to meet the growing demand for its plant-based meat products while maintaining high standards of food safety and product quality. As the company expanded its distribution to over 5,000 restaurants in the U.S. and around 100 in Hong Kong and Macau, it needed to ensure that its manufacturing processes could support this growth. The company required a reliable system to monitor and verify food safety, compliance, and quality control points throughout the production process. Additionally, the company needed to automate quality inspections to maintain consistency and efficiency as it prepared to enter the U.S. grocery market.
Case Study
Revive Kombucha's Journey to Quality and Sustainability with Samsara
Revive Kombucha faced the challenge of scaling its production while maintaining high product quality and sustainability. With rapid growth and national distribution, the company needed to ensure consistent quality across all batches. Additionally, the risk of misprints on lot codes and labels, as well as the need for accurate fill levels, posed significant challenges. The company also aimed to operate more sustainably by monitoring real usage data, such as temperature and water flow, to manage resources efficiently.
Case Study
Enhancing Safety and Efficiency in Bakery Operations: Aunt Millie's Case Study
Aunt Millie’s, a century-old bakery business, faced significant challenges in ensuring worker safety and operational efficiency across its 5 bakeries, 55 distribution centers, and a fleet of 600+ delivery vehicles. The company had a legacy security camera system in place, but it was inefficient and costly. Only a few users could access the footage due to a high license fee per user. Moreover, video retrieval was a time-consuming process, often taking hours to manually find and review footage. This reactive approach to safety incidents was inefficient and in some cases, incidents were not reviewed at all. The company also faced issues with catalytic converter theft. Aunt Millie’s needed a solution that would improve visibility, enable proactive safety measures, and increase back-office efficiency.
Case Study
Liberty Energy: Scaling Innovation with Data and Technology
Liberty Energy, a leader in oilfield services, was faced with the challenge of streamlining their dispersed operations on a single platform and connecting their data and technology. The company's mission is to transform the oil and gas industry in practice and reputation, using technology and data to improve safety, efficiency, and sustainability. However, their existing systems were decentralized and produced inaccurate data, which limited visibility and reporting. Operating in some of the most remote and hazardous environments in the country, Liberty Energy needed a unified solution that would provide accurate, real-time data, ensure the safety of their distributed teams, and improve their operational efficiency.
Case Study
Clover Dairy Uses Samsara to Optimize Fleet Management and Enhance Customer Satisfaction
Given their commitment to excellence, Clover's distribution department decided to evaluate new technologies to optimize deliveries and boost customer service. The team tested several fleet tracking solutions and chose Samsara for its accuracy and real-time updates. Paul Drake, Clover’s Distribution Manager, highlighted that Samsara was chosen because it provides updates right to the minute, unlike other companies that update every 2, 5, or 10 minutes. Samsara helps Clover respond to customer inquiries, remotely control their reefers, analyze delivery progress, and simplify maintenance. The need for real-time tracking was crucial for Clover to handle customer calls efficiently and ensure timely deliveries.
Case Study
Liberty Oilfield Services Enhances Fleet Safety and Efficiency with Samsara
Liberty Oilfield Services faced significant challenges with their previous fleet management system, including GPS drift, inaccurate IFTA mileage reporting, and insufficient customer support. These issues led to wasted time and resources, particularly during inspections or audits. Additionally, Liberty needed a robust communication system for their drivers, especially during convoys, and a reliable solution to improve driver safety in hazardous environments.
Case Study
Birmingham City Schools
With over 20,000 students to transport every day, Birmingham City Schools (BCS) faced significant challenges in managing their large fleet of 158 school buses and 135-vehicle white fleet. The primary issues included improving on-time performance, reducing unsafe driving behavior, and optimizing vehicle maintenance. The previous telematics provider took over 5 months to install devices on new buses, leaving the fleet without real-time data and insights. Additionally, the vehicle-based safety score system was inadequate for tracking individual driver performance, leading to inaccurate assessments and difficulties in driver accountability. Foster, the Director of Transportation, needed a more efficient and reliable telematics solution to address these challenges and improve overall fleet safety and efficiency.
Case Study
KS Industries Enhances Safety and Efficiency with Samsara's Real-Time GPS and Dash Cams
KS Industries (KSI) operates across six major energy-producing states in the United States, managing over 1,200 vehicles and 1,000 drivers. The company needed to enhance safety and visibility for its crews working in remote and hazardous oil fields. The previous system had limitations, including a 100-vehicle cap on live map visibility and connectivity issues in the field. These challenges made it difficult to monitor real-time GPS locations, track crews for rescues, and ensure safety compliance. Additionally, the lack of connectivity hindered productivity, causing delays in processing critical paperwork like Standard Operating Procedures (SOPs) and safety audits.
Case Study
ConGlobal's Pioneering Journey Towards Fleet Electrification
ConGlobal, one of the largest transportation support companies in the U.S., was faced with the challenge of transitioning towards sustainable operations. The transportation and logistics industry is a significant contributor to CO2 emissions, and recent legislation has been pushing for a reduction in greenhouse gas emissions from private sector operations. ConGlobal, however, has always been proactive in its approach towards sustainability, staying ahead of government-imposed regulations and timelines. They were particularly interested in transitioning from diesel to electric vehicles (EVs). However, this transition represented a significant investment of time and resources, especially considering the diverse needs of ConGlobal’s mixed fleet. They needed a systematic, data-driven plan for electrifying their fleet, starting with a pilot.
Case Study
Maximizing Fleet Operations: A Unified Approach by Dohrn Transfer Company
Dohrn Transfer Company, a less-than-truckload carrier providing trucking services and local delivery across the United States, faced a challenge in unifying their data to improve safety and operational efficiency across their organization. Initially, they were seeking a modern, driver-friendly solution to ensure their fleet of over 600 assets remained compliant with ELD regulations as they operated across 14 states and 22 terminals. However, as they evaluated various providers, they realized their needs extended beyond just ELD compliance. Dohrn sought an integrated solution that could connect their data and consolidate their fleet operations in a single platform. They saw an opportunity to leverage real-time data to improve operations such as trailer management, chain of custody, dispatch, maintenance diagnostics, fuel usage, and driver safety.
Case Study
Empowering Fleet Management with IoT: A Case Study on Fraikin UK and Samsara
Fraikin Ltd, one of the largest providers of commercial vehicle contract hire and rental solutions in the UK, was seeking to differentiate itself in the market. The company aimed to evolve from being a mere supplier of vehicles to a provider of comprehensive fleet management solutions. To achieve this, Fraikin needed a way to measure and analyze critical data insights that could help its 200+ customers optimize their fleet operations. The challenge was to find a solution that could provide actionable data on various aspects of fleet management, including mileage, fuel efficiency, idling ratio, and vehicle downtime. The solution also needed to be easy to install and user-friendly, causing minimal disruption to the customers' operations.
Case Study
J. Polep Distribution Ensures Food Safety with Samsara’s Temperature Monitoring for Fleets
Jon Lasko, Director of Transportation, identified a significant opportunity for improvement in J. Polep's cold chain procedures. The loading dock staff was using temperature guns combined with a 2G trailer tracking application to read temperatures of their multi-temp trailers before loading food shipments. The inaccuracy of the guns and the trailer tracking solution with long-delayed reporting and off-hours alerts disturbing staff while at home were major issues. Lasko knew there had to be a better way to ensure food safety and quality.
Case Study
Samsara for Food & Beverage: Schwebel’s Case Study
One of Schwebel’s challenges was maximizing driver productivity. It was not uncommon for routes to be delayed, as drivers made unplanned detours and stops on their way to sales agencies. Because Schwebel’s drivers are paid hourly, delayed routes result in higher costs and more unpredictable customer wait times. Schwebel’s previously relied on a passive GPS solution to track drivers’ routes; however, data from that system could only be synced via WiFi, which could only happen once deliveries were complete. As a result, the distribution team only saw drivers’ routes and stops at the end of the day. It was difficult to see when drivers deviated from their routes, where they tended to go off course, and how long they were delayed. By the time the distribution team noticed deviations, routes were complete and there was no way to make up for lost time. Adam knew that it was time to invest in a more robust solution.
Case Study
Hanson Distillery Partners with Samsara to Automate Quality Checks for Premium Vodka Production
The Hanson family, owners of Hanson of Sonoma, a premium craft vodka distillery, faced significant challenges in maintaining the high quality and precise packaging of their award-winning products. Their commitment to quality required rigorous quality checks, especially for label placement and fill levels, which were manually intensive and inefficient. The production process involved six labels on each bottle, with exact placement and height requirements for the cork and labels. This manual process was time-consuming and prone to errors, making it difficult to scale production efficiently without compromising on quality.
Case Study
Improving Driver Safety with IoT: A Case Study on Chalk Mountain Services
Chalk Mountain Services, a leader in the oilfield services industry, was facing a significant challenge with driver safety. The company, which manages the transportation and logistics of sand and water across Texas and New Mexico, had limited visibility into the safety of their drivers on the road. This lack of insight was leading to preventable accidents and unnecessary worker’s compensation payouts, which were costing the business significantly. Without video evidence, Chalk Mountain was unable to exonerate innocent drivers from not-at-fault accidents and false claims. The company was in search of a solution that would not only enhance driver safety but also engage drivers in the process.
Case Study
Empowering Drivers to Enhance Safety: A Case Study on Eurovia USA and Samsara
Eurovia USA, a company with a fleet of over 2,000 vehicles engaged in roadway maintenance, faced a significant challenge in ensuring the safety of their drivers. The company suspected that unsafe in-cab activities, particularly mobile usage, were leading to an increase in incidents. Additionally, they needed to ensure that seatbelts were being worn consistently to protect drivers from potential injuries. However, without visibility into the cab, Eurovia USA was unable to identify the causes of safety incidents or risky behaviors. They were in need of a proactive safety solution that could improve in-cab visibility, provide real-time feedback for risky behaviors, and empower drivers to improve their habits on the road before an incident occurred.
Case Study
Otto Car Enhances Driver Safety with Samsara's AI-Powered Solutions
Otto Car, London’s largest provider of private hire cars, was facing a significant challenge in ensuring the safety of its drivers and passengers. The company supports over 8,000 rideshare drivers, providing services ranging from licensing to claims advice to driver coaching. As an official partner of Uber, Free Now, and Bolt, Otto Car lends PCO cars to private hire drivers across the UK, making safety a top priority. However, the company was struggling with unreliable telematics and limited data, which hindered its ability to accurately monitor driver safety and provide effective driver coaching to improve it. The lack of reliable data made it difficult for Otto Car to identify high-risk drivers and take appropriate action to mitigate risks.
Case Study
U.S. Logistics Solutions Empowers Drivers with Mobile-First Technology, Saving Time and Money
U.S. Logistics Solutions, a final-mile logistics company, was facing significant challenges due to their use of several disconnected, legacy systems. These systems were inefficient, provided limited visibility into their operations, and lacked customizability for their workforce. The company's processes were largely manual and relied on paper logs and reports, which were error-prone and time-consuming. Lack of visibility from the cab to their warehouses posed another challenge. Without insight into how their drivers were performing or what was happening in their terminals, training opportunities for their team were limited. The company needed an advanced solution to improve their productivity, safety, and employees’ experience.
Case Study
Transforming Driver Workflows: A Case Study on UniGroup and Samsara
UniGroup, a $1.5 billion transportation cooperative, faced a unique challenge due to its complex organizational model. The cooperative, which handles one-third of all professional moves in the United States, is owned by over 160 member agencies. This structure necessitates that their drivers switch between multiple operating authorities (MOAs), complicating the tracking of miles and hours of service (HOS). The need to streamline HOS management and maintain compliance with federal regulations was paramount. However, the solution had to be easy to install and capable of innovating alongside UniGroup's evolving needs.
Case Study
Univar Solutions: Leveraging IoT for Competitive Advantage
Univar Solutions, one of the world’s largest chemical and ingredient distributors, was facing a significant challenge. Their data was siloed across different systems, making it difficult to drive efficiency and safety improvements at scale. This was hindering their innovation and agility. The company was in dire need of upgrading their compliance solution and was seeking a technology partner that could provide a range of applications that would scale and evolve with their needs. Market challenges, such as labor shortage and international supply chain delays, further intensified their resolve to invest in innovative technology to capture and act on critical data in real time.
Case Study
ULC Limos Keeps Customer Service High with Samsara's Real-Time Fleet Management
A vehicle running out of fuel or breaking down is a costly issue for any industry, but it's a nightmare scenario for limousine companies. With such a large fleet, the whole ULC team needs to ensure their custom-designed vehicles are in tip-top shape before going out to chauffeur guests. Before finding Samsara, Jacobian and the ULC team would routinely walk from limo to limo, manually checking and recording the fuel levels and check engine lights before each shift. Jacobian knew there had to be a better way. Jacobian tried fleet management providers with complex interfaces, but needed an easy to use solution. When a friend told him about Samsara, he knew he had to try it.
Case Study
Samsara for Freight and Distribution
Francisco, in his new role at Fames Transport, aimed to modernize the family business to keep up with changing technology and business tools. His first initiative was to update the company's GPS tracking solution, which was clunky and used excessive data. Francisco tasked his team with finding a new provider as soon as their contract finished. Upon discovering Samsara’s platform, he was impressed by its intuitive interface and accurate live location tracking. However, the decision to adopt Samsara was ultimately driven by the platform's comprehensive features, including safety improvements from in-vehicle cameras and operational savings from automating time sheets.
Case Study
Simco Logistics Enhances Safety and Compliance with Samsara Solutions
Simco Logistics, a major ice cream distributor in the Mid-Atlantic, faced challenges in improving fleet safety and complying with the FDA Food Safety Modernization Act (FSMA). Despite having a fleet safety program for over 30 years, the company saw an opportunity to enhance its safety record and reduce accident-related costs. Additionally, as a distributor of temperature-sensitive goods, Simco needed to ensure compliance with FSMA regulations, which required meticulous temperature records during deliveries to prove that food was kept at safe conditions. The company sought a solution that could address both safety and compliance needs effectively.
Case Study
Windy City Limousine & Bus Enhances Customer Experience and Safety with Samsara
Windy City Limousine & Bus faced significant challenges in managing their fleet and ensuring customer satisfaction. The dispatch department was overwhelmed with calls from customers inquiring about vehicle locations, especially during peak hours. The existing GPS tracking system was unreliable, leading to inefficiencies and delays in providing accurate information. Additionally, ensuring passenger safety was a top priority, but the existing safety monitoring system was reactive, relying on customer feedback and delayed video footage. The company needed a solution to provide real-time data, improve safety measures, and enhance overall operational efficiency.
Case Study
City of Jersey Village Enhances Wastewater Management with Samsara SCADA System
Prior to engaging with Samsara, Garcia and his team had no advanced warning of lift station issues until they made the journey on-site. This lack of forewarning led to significant equipment damage and high repair costs. For instance, a dry well filled with raw water corroded equipment, costing over $70,000 in repairs. The absence of alarms and notifications meant that issues were only discovered during on-site visits, making it difficult to prevent incidents like flooding. This reactive approach was inefficient and costly, prompting the need for a more proactive solution.
Case Study
Optimizing Safety and Efficiency in Transportation: A Case Study on All Aboard America
All Aboard America (AAA), a passenger transportation company operating private charters and public routes in three states, was facing challenges with their disconnected, manual processes that strained resources and limited data-backed decision making. They were using disparate, legacy systems for reporting, driver coaching, and tracking the efficiency and health of their fleet. Without access to detailed data from a single source of truth, making informed business decisions was a challenge. AAA needed a solution that would connect their operations to provide greater data insights, streamline administrative work, and proactively ensure the safety of their drivers and passengers.
Case Study
M Group Services Enhances Fleet Safety with Samsara's IoT Solutions
M Group Services Plant & Fleet Solutions (MGSPFS), a leading infrastructure services provider in the UK and Ireland, faced a significant challenge in reducing road traffic incidents involving their fleet. With a large number of vehicles on the road at any given time, the company needed to enhance its visibility of road incidents to preemptively prevent them. The goal was not only to ensure the safety of their drivers but also to reduce related insurance premiums. Despite having a strong culture of safety and efficiency, the lack of real-time monitoring and predictive insights made it difficult for MGSPFS to achieve its safety objectives.
Case Study
Roto-Rooter's Investment in Safety at Scale with Samsara
Roto-Rooter, a leading plumbing and water clean-up company in the United States, faced a significant challenge in managing the safety of its large fleet of service vehicles. With over 1,200 drivers constantly on the move, the company needed a solution that would allow them to communicate with drivers effectively while also ensuring their safety. The company's operations, which involved dispatching vehicles based on timing, proximity, and urgency, were primarily conducted on mobile devices. This led to issues with driver distraction. The company needed a solution that would allow them to communicate with drivers while also protecting them from distractions. The challenge was to find a solution that would enable them to invest in safety at scale.
Case Study
Improving Safety and Reducing Liability in Taxi & Limousine Services with IoT
Aeroport Taxi & Limousine Services, a large fleet management company in Ontario, Canada, was facing significant challenges in managing driver safety and liability across its fleet of over 3,000 vehicles and drivers. The company's previous dash cam vendor had limitations that didn't meet their needs. The footage was automatically overwritten once the dash cam's memory card reached capacity, making it difficult to investigate incidents and refute false claims. Additionally, the lack of in-cab alerts meant that drivers could only be coached after an incident had already occurred. This lack of real-time feedback and visibility into incidents put Aeroport at risk for false claims and increased insurance costs. Aeroport needed a solution that could provide real-time feedback for drivers and better visibility into incidents to improve safety and protect their business.
Case Study
Holiday Tours
Holiday Tours, a family-owned charter bus company, faced challenges in managing their fleet operations efficiently. Despite having a custom-built system for managing customer reservations, scheduling, maintenance, accounting, and HR, they lacked a way to accurately pinpoint the location of their buses. This gap in their system made it difficult to provide real-time updates to customers about bus locations, which was particularly problematic in city environments where a two-minute delay could mean a difference of 10 blocks. Additionally, their existing camera system only collected harsh driving events in large batches during the evening, limiting their ability to provide instant feedback on driver behavior and customer experience. The company also needed a more efficient way to manage maintenance, as motorcoaches require regular maintenance to deal with diesel particulates through a process called regeneration. Not performing regeneration on time could cause the vehicle to stop, posing a significant operational risk.
Case Study
Collins Earthworks Enhances Fleet Management with Samsara's Integrated Solutions
Collins Earthworks, a rapidly growing earthmoving business, faced challenges with their previous telematics system, which was insufficient for their expanding needs. The old system was primarily used to track the location of trucks, but as the company grew, they required a more comprehensive solution to enhance productivity, efficiency, and safety. The need for a better system became evident when they realized that their existing telematics could not provide the necessary insights and data to manage their fleet effectively. This led them to search for a new solution that could meet their evolving requirements and support their growth trajectory.
Case Study
KeHE Distributors Leverages Samsara for Fleet Efficiency and Safety
KeHE Distributors faced challenges with their previous AOBRD and GPS tracking provider, which had hardware that was difficult to install and use. The hardware was not portable, leading to a loss of GPS tracking on 15% of their fleet, making it difficult to accurately track deliveries and update customers with ETAs. Additionally, drivers struggled with the in-cab tablets provided by the previous system, which could not load additional apps, resulting in a lack of a consolidated place to track routes and hours. This led to inefficiencies and a cluttered electronic setup in the trucks.
Case Study
CR Jackson's Transformation: Saving $120K with Integrated IoT Asset Tracking
CR Jackson, a South Carolina-based infrastructure company, was facing significant operational challenges due to the lack of a unified system for managing their equipment, vehicles, drivers, and back-office operations. They were using multiple vendors for compliance management, equipment tracking, and light fleet management, which resulted in scattered processes across different systems and paperwork. This lack of integration led to issues around asset protection, driver exoneration, and operational inefficiency. The company had also experienced theft of expensive equipment on multiple occasions, which further emphasized the need for a robust and cost-effective tracking solution. They needed a single integrated platform that could unify their mission-critical processes and provide real-time visibility across their assets.
Case Study
Hoskins Equipment: Achieving Operational Excellence through Unified IoT Approach
Hoskins Equipment, a leader in high-reach equipment rentals, was facing a challenge in maintaining their standard of operational excellence across their 1,400 pieces of equipment, 30 vehicles, and multiple sites. The company lacked clear visibility into their physical operations and needed a way to operate more efficiently. They were seeking a solution that would enable them to stretch their resources further and work better and faster. The company saw an opportunity to digitize their processes and take a unified approach to their operations across their drivers, assets, and facilities. They were in search of an integrated solution that could consolidate these solutions within a single platform, thereby maximizing efficiency and centralizing their operations.
Case Study
Building a Culture of Safety: A Case Study on PODS Moving & Storage
PODS Moving & Storage, a national moving and storage company operating across the United States and Canada, faced a significant challenge in ensuring the safety of their drivers and the belongings they transported. The company had no real-time data or visibility into the status of their drivers, making it difficult to engage with them actively, coach them on risky behavior, or acknowledge their performance improvements. The existing solution did not provide fleet managers with real-time data, which was a significant hindrance in case of accidents or driver injuries. The lack of immediate assistance and feedback mechanisms led to less than satisfactory driving.
Case Study
Road Commission of Kalamazoo County's Transformation with IoT: A $60K Saving Case Study
The Road Commission of Kalamazoo County (RCKC) is tasked with maintaining over 1,200 miles of road, 63 bridges, more than 27,000 road signs, and numerous traffic signals across Kalamazoo County, Michigan. Their work ranges from road maintenance to asset management, township relations, and safety service requests. Prior to implementing Samsara, the RCKC was using a legacy GPS provider that was unreliable and limited in its functionality. Their team relied on paper-based workflows for driver vehicle inspection reports (DVIRs), which led to reactive equipment maintenance, unexpected downtime, and costly repairs. The RCKC was in need of a more efficient way to manage their expansive operations, seeking a technology partner that could enhance their operations from end to end, and empower their personnel and the community they serve.
Case Study
Enhancing Operational Efficiency and Security with IoT: A Case Study on Teichert
Teichert, a California-based construction and materials producer company, faced significant challenges due to limited visibility across its vast operations. With over 30 locations, hundreds of vehicles, and thousands of employees, real-time visibility into their entire operations was critical. The company was heavily reliant on its assets and materials for its work, making it essential to ensure adequate resources were available and located where needed. The company was also grappling with ongoing thefts, which necessitated an easy-to-use camera solution to help them quickly investigate, resolve, and prevent future thefts. The lack of an efficient system led to countless hours spent reviewing video footage, which was both time-consuming and inefficient.
Case Study
Case Study: Cowgirl Creamery
Cheese is a comparatively difficult product to produce, store, and ship. Each variety requires different aging times, temperature, and humidity. The same goes for shipping, and it is imperative that cheese is protected from high temperatures and humidity due the effect on delicate flavors and the potential for bacterial growth. The Cowgirl Creamery team was using analog temperature and manually recording temperatures on clipboards three times a day in their delivery trucks and twice daily in their aging rooms, cold storage rooms, and milk tanks. Cunnie knew there had to be a better way to record all this data, and she began looking at chart recorders to record temperature and alert the team when temps fell out of spec. Coincidentally, Cunnie was also searching for a fleet management solution to improve the operations of their distribution network. She hoped to find a solution that combined temperature monitoring with fleet management. That’s when she found Samsara.
Case Study
Case Study: Acme Smoked Fish
Hartmann and his team sought a way to track the temperature and location of their refrigerated shipments to ensure quality upon delivery to their 1,800 accounts between New England and Philadelphia. Acme’s ongoing commitment to product safety, along with their esteemed BRC Certification, made documenting temperature throughout the cold chain critical. Specifically, Hartmann was looking for a solution with accurate temperature monitoring and real-time alerting that was easy to use. The Acme team was using thousands of basic data loggers which were quickly lost or damaged during operation. When the data loggers failed, the corresponding deliveries were rejected. “This is a big hassle and very expensive,” comments Hartmann. For Acme, this equates to tens of thousands of dollars lost annually due to waste, extra shipments, and labor.
Case Study
Bellas Landscaping Streamlines Operations with Samsara’s Real-Time Fleet Tracking Solution
Bellas Landscaping, a leading landscaping firm in central Illinois, faced significant challenges in managing their fleet of over 30 vehicles. The fleet, which includes dump trucks, flatbeds, and pickups, is crucial for their operations, especially during the busy seasons. The company needed a solution to improve fleet visibility, reduce idle times, and enhance overall operational efficiency. Additionally, they sought to optimize maintenance schedules and refueling processes to cut down on unnecessary costs and improve productivity.
Case Study
Samsara's Integrated Platform Saves Moore Food Distributors Over $250,000 After Major Accident
In October 2017, Moore Food Distributors faced a significant challenge when one of their trucks was involved in a major accident. The truck was traveling on the highway at 65 mph when it was struck by a car, causing it to tip over, pass through the guardrail, and fall down an embankment. This incident posed a serious risk to the company's operations and financial stability. The immediate need was to prove that their driver was not at fault to avoid potential legal and insurance complications. Additionally, Moore Food Distributors needed to ensure the safety of their fleet and compliance with the Food Safety Modernization Act (FSMA). The company required a robust solution to provide real-time data on vehicle location, driving behavior, and environmental conditions to enhance fleet safety and customer service.
Case Study
Dohrn Transfer Company Utilizes Samsara for Fleet Management and Safety Improvements
Dohrn Transfer Company needed a solution for ELD compliance and broader business initiatives such as improving safety, reducing paperwork, optimizing maintenance, and enhancing dispatching efficiency. The company was subject to Hours of Service regulations and required a reliable system to ensure compliance. Additionally, Dohrn wanted a user-friendly and flexible platform that could integrate seamlessly with their existing operations and engage employees effectively.
Case Study
Cardinal Plumbing Enhances Fleet Operations with Samsara Solutions
Cardinal Plumbing faced the challenge of managing a growing fleet while ensuring operational efficiency and maintaining a high level of customer service. With the expansion of their services to include heating and cooling, the need for a robust fleet management solution became even more critical. The company needed a way to gain real-time visibility into their fleet operations, streamline maintenance processes, and protect their brand reputation by promoting safe driving practices among their technicians.
Case Study
Markstein Sales Company Improves Fleet Safety and Saves Money with Samsara Dash Cams
After a few accidents served as a wake-up call that their current safety program wasn’t working, Markstein knew they needed to do something more to improve their fleet safety. Director of Operations Tom Roberts began looking for a dash cam solution that would help him save money, exonerate his drivers from accidents, and coach drivers on defensive driving tactics. Getting driver buy-in on dash cams from day one was a significant challenge. Roberts found a way to get his drivers excited about dash cams by selecting his top driver to pilot the system and provide initial feedback. This approach helped in getting the drivers to be advocates of the system.
Case Study
Central Texas Water Supply
Central Texas Water Supply faced frequent connectivity issues with their legacy SCADA system, which was critical for monitoring and controlling their water supply operations. The system's reliance on two-way radios led to delays in receiving updates, especially during bad weather, causing significant communication gaps. Additionally, the SCADA provider was closing its doors, necessitating a switch to a more reliable and efficient solution. The organization needed a system that could provide real-time monitoring, prevent service interruptions, and improve operator efficiency.
Case Study
Berkeley County School District Enhances Student Safety and Streamlines Parent Communication with IoT
Berkeley County School District in West Virginia, responsible for transporting over 17,000 students daily, faced significant challenges in ensuring student safety and efficient communication with parents. The district had limited visibility into the real-time location of their school buses, making it difficult to monitor and respond to safety concerns. Their existing camera system offered only basic functionality, and retrieving footage was a time-consuming process. This lack of real-time visibility made it difficult to detect and address risky driving behaviors. Furthermore, parents often raised concerns about school bus delays and student safety, but due to the lag time from their legacy GPS vendor, the district was unable to provide accurate and timely information. Each safety concern call took up to 15 minutes to investigate, highlighting the need for a more efficient solution.
Case Study
Brothers Food Services Enhances Safety and Efficiency with Site Visibility
Brothers Food Services (BFS), one of the largest produce distributors in Texas, faced a significant challenge in maintaining employee safety across their vast operations. With over 500,000 square feet of warehousing space spread across four main distribution centers, BFS needed a system that could streamline incident investigation and save labor hours. Their previous camera systems were time-consuming and inefficient, often taking hours to locate the correct video footage for incident investigation. This reactive approach was not only labor-intensive but also hindered their ability to promptly address safety incidents.
Case Study
Enhancing Efficiency and Compliance in Atlanta's Aviation Department through IoT
The City of Atlanta's Department of Aviation is tasked with maintaining the vast land surrounding the Atlanta Airport, the busiest airport globally. A critical part of this maintenance involves keeping the grass mowed to a specific height as per FAA regulations to prevent attracting wildlife like birds, which pose a safety risk to aircraft. However, the department faced significant challenges in ensuring this compliance due to limited visibility into the mowing operations. They relied on manual work orders and line-of-sight supervision, which did not provide any means to confirm whether the grass was mowed correctly or even mowed at all unless a supervisor was physically present to oversee the process.
Case Study
Improving Driver Safety with IoT: A Case Study on Foundation Building Materials
Foundation Building Materials (FBM), one of North America's leading distributors of building materials, prioritizes safety as its core value. With a fleet of 4,500 vehicles and heavy equipment, and over 5,500 employees across 270+ branches, maintaining driver safety and training is a significant challenge. As the company grew, it faced difficulties in scaling its safety programs due to the limitations of its legacy telematics and scheduling systems. These systems were not integrated with their driver safety program, making it challenging to gain insights into driver performance. The need for better technology to enhance visibility into driver performance and safety became increasingly apparent.
Case Study
Papa & Barkley's Transformation of Onsite Operations with Samsara Site Visibility
Papa & Barkley, a cannabis manufacturer and distributor, faced significant challenges in managing their facilities. With four different facilities primarily located in Eureka, California, they had to adhere to strict safety requirements and specialized regulations for the cannabis industry. This necessitated real-time visibility and facility security. To ensure compliance and safety, they employed Facility Intelligence Coordinators (FICs) to monitor their operations 24/7 using a legacy camera system. However, with 167 cameras monitoring a collective 79,000 square feet, manually reviewing footage was time-consuming and led to burnout among the FICs. Additionally, the City of Eureka and the state of California conducted surprise inspections, for which retrieving video footage was essential. Before Samsara, finding the right footage could take hours. As a rapidly growing company, Papa & Barkley needed an onsite camera system that could streamline their processes and scale with them.
Case Study
Enhancing Technician Safety and Operational Efficiency: A Case Study on Satellites Unlimited
Satellites Unlimited (SUI), a leading regional service provider for a major national satellite company, was facing significant challenges in building a cutting-edge safety program. The company's safety program was largely based on anecdotal evidence from technicians and managers, which did not allow them to reliably identify the root cause of safety incidents. This became a pressing issue when SUI experienced two catastrophic vehicle incidents, resulting in multi-million dollar worker’s compensation claims. The company was aware of issues such as tailgating and distracted driving, but lacked the means to prove it. Therefore, SUI sought a solution that would provide an unbiased source of truth about what was happening in the cab when technicians were out on the road.
Case Study
Van der Linden Enhances Driver Safety and Avoids Fines with Samsara
Van der Linden, a 125-year-old road transportation company based in the Netherlands, was facing a significant challenge due to outdated systems. The company, which specializes in dedicated delivery services, was struggling to monitor driver hours and maintain compliance with EU rules. In the Netherlands, if a driver is fined for driving too many hours without observing the mandatory rest periods, the employer is required to pay a fine double that amount. With the minimum fine for drivers set at €220, Van der Linden was at risk of incurring substantial costs from non-compliance across its growing fleet. The company's traditional method of drivers clocking in with timecards and manually reporting monthly truck data was proving to be inefficient and error-prone.
Case Study
Charles King Company Enhances Pump Uptime with Samsara's Remote Monitoring Solutions
Charles King Company’s pumping systems are critical for emergency and planned projects in treatment plants, pump stations, and collection systems. Any downtime can result in sewage overflows, leading to regulatory fines and environmental consequences. The company needed a reliable solution to monitor pump systems 24/7 to prevent overflows and ensure system reliability. They previously used analog auto-dialers for alerts, which were limited in functionality and only provided emergency-level notifications.
Case Study
The City of Cocoa Fleet Management Division relies on Samsara to increase visibility and efficiency across their municipal fleet.
The Cocoa Fleet Team needed better visibility across the city’s 400 vehicles. They were using an offline GPS system that only provided telematics data when vehicles refueled, which was inefficient. They required scheduled reports, geofencing, real-time vehicle location, and the ability to link drivers to vehicles. The team needed a faster way to get this data and ensure that all vehicles and personnel operated efficiently and safely.
Case Study
Blue Lightning Logistics Uses Samsara for Enhanced Fleet and Temperature Control
Blue Lightning Logistics faced significant challenges in monitoring their fleet and maintaining temperature control for their temperature-sensitive loads. The company was losing $30,000 to $50,000 annually due to rejected loads caused by temperature fluctuations and lack of real-time monitoring. Additionally, the company had no way to track the location of their trailers, leading to operational inefficiencies and increased risk of theft.
Case Study
Ghilotti Bros., Inc. Enhances Efficiency and Safety with Samsara's Integrated Fleet Management System
When company leaders started looking for a new fleet management system in 2017, they knew they wanted more than GPS location tracking. Ghilotti Bros. also wanted to find an integrated solution that would help protect their 175 employees, their equipment, and their brand. The company needed a system that could provide real-time visibility into their operations, streamline maintenance processes, and enhance safety measures. With a large fleet and numerous high-value construction equipment spread across multiple job sites, tracking and maintaining these assets efficiently was a significant challenge. Additionally, ensuring the safety of their employees in one of the most dangerous occupations in the United States was a top priority.
Case Study
Deschutes Brewery Partners with Samsara for Equipment Monitoring and Optimization
Deschutes Brewery faced a potential $750,000 investment in a redundant chiller to ensure the reliability of their brewing process. To avoid this significant capital expenditure, they needed a way to assess the health of their existing chiller and make informed decisions about its maintenance and operation. The challenge was to find a solution that could provide real-time insights into the chiller's condition and help optimize its usage to extend its lifespan.
Case Study
Meridian Brick Partners with Samsara to Enhance Production Efficiency with Real-Time Data
When a single hour of downtime at Meridian Brick costs thousands of dollars in lost revenue, having the most accurate downtime data is critical for the company’s bottom line. David Peters, Meridian Brick’s Director of Technical Services, is on a mission to improve operational efficiency, and knows that accurate production data is the first step in knowing what to improve. The most challenging part of their manual data logging process was never having accurate times. All of the 30-second downtimes that went unlogged ended up becoming death by a thousand papercuts. With Samsara, the impact of real-time analytics on uptime, throughput, and scrap rate that can be accessed from any device has been immediate. The data is way more accurate than what was possible with a manual system. They noticed, for example, that a significant amount of downtime was occurring at a particular plant due to raw material loading, something which wasn’t apparent in their manual data before. Accurate downtime logging has empowered David and the plant managers to make more informed decisions around processes, resourcing, and capital expenditures in order to improve production performance.
Case Study
Pine Environmental Partners with Samsara for Enhanced Remote Monitoring Solutions
Pine Environmental's clients needed a more efficient way to monitor and report on various environmental factors such as air, gas, water, and soil quality. Previously, clients had to manually collect data from monitoring equipment spread across large job sites, which was time-consuming and inefficient. Pine sought a telemetry solution that could provide centralized visibility into real-time and historical sensor data. They required a system that was always on, scalable, easy to use, and supported multiple industrial protocols. Additionally, the solution needed to offer secure communications, mobile visibility, and low-powered hardware with data backup capabilities. After unsatisfactory experiences with previous telemetry providers, Pine laid out a no-compromise set of required capabilities for their new system.
Case Study
Digital Transformation of American Cementing: Enhancing Efficiency with IoT
American Cementing, a leader in cementing services for the oil and gas industry, was grappling with inefficiencies in their operations due to manual and paper-based administrative processes. The field technicians had to deal with a plethora of paper documents such as pre-inspection reports and fuel receipts before operating heavy equipment at well sites. This not only increased the chances of human error but also slowed down the process. The back-office team was also burdened with the task of managing the paperwork manually. Additionally, the payroll process was time-consuming and prone to inaccuracies as driver logs and the internal payroll software were not integrated. This led to issues such as inaccurate payments and a lowered employee experience when drivers forgot to log off once they were off duty.
Case Study
Fraley & Schilling's Digital Transformation with Samsara Connected Operations Cloud
Fraley & Schilling (F&S), a premier lightweight fleet operator in the eastern United States, was in need of a unified platform to replace outdated operating models and drive digital transformation across the organization. The company was seeking a technology partner that would empower drivers to own their safety journey, personalize their driver experience, and improve safety. The F&S team also needed to automate vehicle and equipment monitoring capabilities to replace unreliable and labor-intensive spreadsheets. The challenge was to ensure continuous driver experience improvements in a competitive market and to build a world-class driver experience.
Case Study
Case Study: KWRL Transportation Co-Op
KWRL Transportation Cooperative, the largest school bus fleet in Washington state, faced significant challenges in managing its 100 buses and ensuring the safety and efficiency of its operations. The existing repeater-based GPS system was inadequate, providing updates every 10 minutes, which was insufficient for real-time monitoring. This lack of real-time visibility made it difficult for the team to keep buses on route and on time, leading to inefficiencies and potential safety risks. Additionally, the cooperative needed a solution that could handle the growing number of students and routes, as one of the districts was projected to grow from 2,000 to 8,000 students by 2025. The team also required accurate historical data to build smarter routes and plan for fleet expansion, as well as real-time alerts for engine fault codes to ensure timely maintenance and reduce downtime.
Case Study
Mountain Eagle Trucking Enhances Fleet Management and Compliance with Samsara Solutions
Mountain Eagle Trucking faced several challenges in managing their fleet operations across the Canada-United States border. The company needed to ensure timely deliveries and pickups to maintain high customer satisfaction. Additionally, they had to manage the safety and compliance of their fleet, including temperature monitoring for food and beverage distribution to prevent rejected loads. The cross-border operations also required compliance with different regulations and laws in Canada and the U.S., making it essential to have accurate tracking and reporting systems in place.
Case Study
Coshocton Trucking's Digital Transformation: Saving $650K+ in Insurance and Fuel Costs
Coshocton Trucking, a transportation service provider in the U.S. for over 30 years, was grappling with outdated operational technology and manual processes. The company's operations were hampered by a lack of visibility into key areas such as fuel usage and driver safety, which led to increased costs and inefficiencies. The introduction of Hours of Service (HOS) regulations by the FMCSA further complicated matters, as Coshocton's paper-based processes were ill-equipped to handle the assignment and monitoring of driver hours. Rising fuel costs and growing operations exacerbated the problem, with the company unable to reduce idling and minimize costs due to limited visibility into fuel consumption. Additionally, a reactive approach to driver safety led to risky driving behaviors and thousands of dollars in insurance claims. To support their growing business, Coshocton needed to modernize their technology stack to improve safety, efficiency, and competitiveness.
同类供应商.
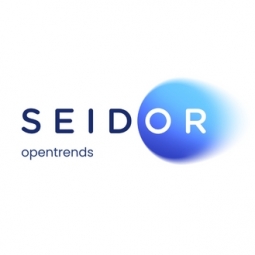
Supplier
Opentrends
Opentrends provides the most advanced custom software solutions to place companies in the Digital Transformation path, allowing them to achieve innovation advantage and contribute to their growth acceleration.More than 18 years delivering innovative projects of high technological complexity in a wide range of industries, while guaranteeing quality and alignment with our client’s objectives. In fact, over a hundred global companies across various industries have full Trust in our unique ability to design, build, implement, and integrate complex software innovations into their organizations.Let’s excel your digital future today.
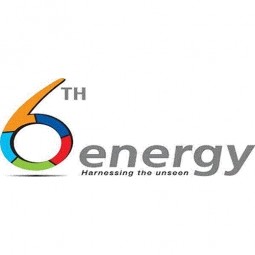
Supplier
Sixth Energy Technologies Private Limited
6th Energy Technologies is a leading Energy, Environment and Water Data Intelligence Company. Their current focus is on providing end-to-end remote management solutions for Data Centers, Businesses, Banks, Telecom and Enterprise Infrastructures. They remotely monitor and manage power and cooling equipment in telecom towers (BSC, BTS), telecom switching centers (MSC), Data centers, Industrial locations, enterprise buildings, off-grid and grid-tie renewable energy power stations, etc. 6th Energy's wireless solutions include collection and analysis of energy and environmental data, mining, creating alerts and reports thereby providing valuable energy optimization and control solutions to their users. Their in-house R&D has created advanced, scalable and robust systems which have been successfully deployed in thousands of locations around the world. Their customers have reported significant operational and commercial benefits, showing ROI within 6 to 10 months. 6th Energy is driven by a core team of professionals with varied educational background and long international experience in the telecom and energy domain. Some of their team members have been part of companies like Ericsson etc. Their team members have authored many patents in their past with many more in the pipeline as part of their R&D work at 6th Energy. Their trademark solution - 6E IoT Platform consists of robust hardware, Firmware, software, and our tools and services.More to Know: https://www.6thenergy.com/
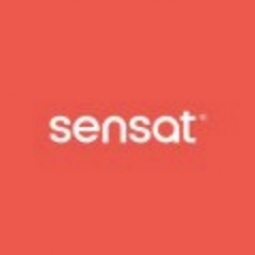
Supplier
SenSat
SenSat turns complex visual and spatial data into a real time simulated reality that helps computers solve real world problems. The cloud-based technology allows companies operating in physical domains, such as infrastructure construction, to make more informed decisions based on multiple variables at large scale and complexity. SenSat call this ??òVisual Intelligence???, a subset of Artificial Intelligence focussed on teaching computers how to understand and interact with the real world.Their simulated realities replicate real-world locations in real time, bringing clarity to complex visual and spatial data. This helps you to make smarter, faster and safer decisions based on real world information. Their cloud-based technology Mapp? allows companies operating in physical domains to make more informed decisions based on multiple variables at large scale and complexity.
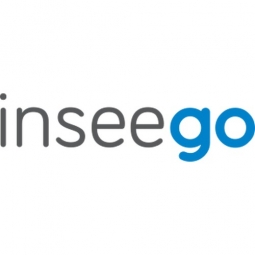
Supplier
Inseego
Inseego is a global provider of software-as-a-service and solutions for the Internet of Things. It sells its telematics solutions under the Ctrack brand, including its fleet management, asset tracking, and monitoring, stolen vehicle recovery, and usage-based insurance platforms. Inseego also sells business connectivity solutions and device management services through Novatel Wireless, Inc. and Feeney Wireless ("FW").
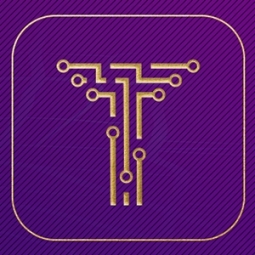
Supplier
TrackoBit
TrackoBit is the fastest growing Telematics software company based out of India. We are determined to expand to every corner of the world and connect the remotest of areas with the latest GPS Tracking technology. We have been in business since 2018. We have covered more than 1100 cities with around 1,00,000 vehicles running on our portal. Our network is growing every day with new vehicles joining in every minute and fresh data coming in every millisecond. Our software works day and night, ensuring impeccable accuracy of data along with the uptime of 99.9% which is one of the best in the industry. Companies riding with us - Amazon India, Maruti Suzuki, Red Bus, Tata Steel, TCI, Bonn Breads and many more.